Schmieden

Es gibt viele verschiedene Arten von Schmiedeprozessen; Sie können jedoch in drei Hauptklassen eingeteilt werden:
- Herausgezogen: Länge nimmt zu, Querschnitt nimmt ab
- Verärgert: Länge nimmt ab, Querschnitt nimmt zu
- In geschlossenen Presswerkzeugen zusammengedrückt: erzeugt multidirektionale Strömung
Gängige Schmiedeverfahren sind: walzschmieden, Gesenkschmieden, Zahnradschmieden, Freiformschmieden, Pressformschmieden (Close die Forging), Pressschmieden, Kaltschmieden, Warmschmieden und Stauchen.
Temperaturbearbeiten
Alle folgenden Schmiedeprozesse können bei verschiedenen Temperaturen durchgeführt werden; Sie werden jedoch im Allgemeinen danach klassifiziert, ob die Metalltemperatur über oder unter der Rekristallisationstemperatur liegt. Wenn die Temperatur über der Rekristallisationstemperatur des Materials liegt, gilt dies als Warmschmieden; wenn die Temperatur unter der Rekristallisationstemperatur des Materials, aber über 30% der Rekristallisationstemperatur (auf einer absoluten Skala) liegt, gilt sie als Warmschmieden; Wenn unter 30% der Rekristallisationstemperatur (normalerweise Raumtemperatur), gilt sie als Kaltschmieden. Der Hauptvorteil des Warmschmiedens besteht darin, dass es schneller und präziser durchgeführt werden kann, und da das Metall verformt wird, werden die Aushärtungseffekte durch den Rekristallisationsprozess negiert. Kaltschmieden führt typischerweise zu einer Kaltverfestigung des Stücks.
Gesenkschmiedearbeit
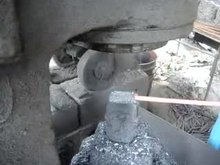
Medien abspielen
Gesenkschmieden ist ein Schmiedeprozess, bei dem ein Hammer angehoben und dann auf das Werkstück „fallen gelassen“ wird, um es entsprechend der Form der Matrize zu verformen. Es gibt zwei Arten von Gesenkschmieden: Gesenkschmieden mit offenem Gesenk und Gesenkschmieden mit tiefem Gesenk (oder geschlossenem Gesenk). Wie die Namen andeuten, liegt der Unterschied in der Form der Matrize, wobei die erstere das Werkstück nicht vollständig umschließt, während die letztere dies tut.
Gesenkschmiedearbeiten


Freiformschmieden wird auch als Schmieden bezeichnet. Beim Freiformschmieden schlägt und verformt ein Hammer das Werkstück, das auf einen stationären Amboss gelegt wird. Das Freiformschmieden hat seinen Namen von der Tatsache, dass die Matrizen (die Oberflächen, die mit dem Werkstück in Kontakt stehen) das Werkstück nicht umschließen und es fließen lassen, außer wenn es von den Matrizen berührt wird. Der Bediener muss daher das Werkstück ausrichten und positionieren, um die gewünschte Form zu erhalten. Die Würfel sind normalerweise in der Form flach, aber einige haben eine besonders geformte Oberfläche für fachkundige Operationen. Beispielsweise kann eine Matrize eine runde, konkave oder konvexe Oberfläche aufweisen oder ein Werkzeug zum Formen von Löchern oder ein Trennwerkzeug sein.Freiformschmiedeteile können in Formen bearbeitet werden, die Scheiben, Naben, Blöcke, Wellen (einschließlich Stufenwellen oder mit Flanschen), Hülsen, Zylinder, Ebenen, Sechsecke, Runden, Platten und einige benutzerdefinierte Formen umfassen.Das Freiformschmieden eignet sich für kleine Auflagen und eignet sich für Kunstschmiede und Maßarbeit. In einigen Fällen kann das Freiformschmieden eingesetzt werden, um Rohblöcke zu formen, um sie für nachfolgende Vorgänge vorzubereiten. Das Freiformschmieden kann das Korn auch ausrichten, um die Festigkeit in der erforderlichen Richtung zu erhöhen.
Vorteile des Freiformschmiedens
- Geringere Wahrscheinlichkeit von Hohlräumen
- Bessere Ermüdungsbeständigkeit
- Verbesserte Mikrostruktur
- Kontinuierlicher Kornfluss
- Feinere Korngröße
- Höhere Festigkeit
- Besseres Ansprechen auf Wärmebehandlung
- Verbesserung der inneren Qualität
- Höhere Zuverlässigkeit der mechanischen Eigenschaften, Duktilität und Schlagfestigkeit
„Cogging“ ist die sukzessive Verformung eines Stabes entlang seiner Länge unter Verwendung einer offenen Gesenkschmiede. Es wird häufig verwendet, um ein Stück Rohmaterial auf die richtige Dicke zu bearbeiten. Sobald die richtige Dicke erreicht ist, wird die richtige Breite durch „Kanten“ erreicht.“Kanten“ ist der Prozess der Materialkonzentration mit einer konkav geformten offenen Matrize. Der Vorgang wird als „Kanten“ bezeichnet, da er normalerweise an den Enden des Werkstücks ausgeführt wird. „Fullering“ ist ein ähnlicher Prozess, der Abschnitte des Schmiedens unter Verwendung eines konvex geformten Gesenks verdünnt. Diese Prozesse bereiten die Werkstücke für weitere Schmiedeprozesse vor.
-
Einfassung
-
Vollständige Abdeckung
Abform-Gesenkschmiedenedit
Abform-Gesenkschmieden wird auch als „Gesenkschmieden“ bezeichnet. Beim Gesenkschmieden wird das Metall in eine Form gelegt, die einer Form ähnelt und an einem Amboss befestigt ist. Normalerweise wird der Hammerstempel auch geformt. Der Hammer wird dann auf das Werkstück fallen gelassen, wodurch das Metall fließt und die Matrizenhohlräume füllt. Der Hammer ist in der Regel in Kontakt mit dem Werkstück auf der Skala von Millisekunden. Abhängig von der Größe und der Komplexität des Teils kann der Hammer mehrmals hintereinander fallen gelassen werden. Überschüssiges Metall wird aus den Formhohlräumen herausgedrückt und bildet einen sogenannten „Blitz“. Der Blitz kühlt schneller ab als der Rest des Materials; Dieses kühle Metall ist stärker als das Metall in der Matrize und verhindert so, dass sich mehr Blitz bildet. Dies zwingt das Metall auch, den Formhohlraum vollständig zu füllen. Nach dem Schmieden wird der Blitz entfernt.
Beim kommerziellen Gesenkschmieden wird das Werkstück normalerweise durch eine Reihe von Hohlräumen in einer Matrize bewegt, um von einem Block in die endgültige Form zu gelangen. Der erste Eindruck wird verwendet, um das Metall in die raue Form entsprechend den Bedürfnissen der späteren Hohlräume zu verteilen; Dieser Eindruck wird als „Kanten“, „schiefen“ oder „Biegen“ Eindruck. Die folgenden Hohlräume werden als „blockierende“ Hohlräume bezeichnet, in denen das Stück in eine Form gebracht wird, die dem Endprodukt ähnlicher ist. Diese Stufen verleihen dem Werkstück normalerweise großzügige Biegungen und große Filets. Die endgültige Form wird in einem „Final“ – oder „Finisher“ -Abformhohlraum geschmiedet. Wenn nur eine kurze Stückzahl von Teilen zu erledigen ist, kann es wirtschaftlicher sein, wenn der Matrize ein endgültiger Abdruckhohlraum fehlt und stattdessen die endgültigen Merkmale bearbeitet werden.
Das Gesenkschmieden wurde in den letzten Jahren durch eine zunehmende Automatisierung verbessert, die Induktionserwärmung, mechanische Zuführung, Positionierung und Manipulation sowie die direkte Wärmebehandlung von Teilen nach dem Schmieden umfasst.Eine Variante des Gesenkschmiedens wird als „blitzloses Schmieden“ oder „echtes Gesenkschmieden“ bezeichnet. Bei dieser Art des Schmiedens sind die Matrizenhohlräume vollständig geschlossen, wodurch verhindert wird, dass das Werkstück einen Blitz bildet. Der Hauptvorteil dieses Prozesses ist, dass weniger Metall durch Blitz verloren geht. Flash kann 20 bis 45% des Ausgangsmaterials ausmachen. Zu den Nachteilen dieses Verfahrens gehören zusätzliche Kosten aufgrund eines komplexeren Werkzeugdesigns und der Notwendigkeit einer besseren Schmierung und Werkstückplatzierung.
Es gibt andere Variationen der Teilebildung, die das Gesenkschmieden integrieren. Ein Verfahren beinhaltet das Gießen eines Schmiedevorformlings aus flüssigem Metall. Das Gussteil wird nach dem Erstarren entfernt, jedoch noch heiß. Es wird dann in einem einzigen Hohlraum sterben fertig. Der Blitz wird getrimmt, dann wird das Teil Quench gehärtet. Eine andere Variante folgt dem gleichen Verfahren wie oben beschrieben, mit der Ausnahme, dass die Vorform durch Aufsprühen von Metalltröpfchen in geformte Kollektoren hergestellt wird (ähnlich dem Osprey-Verfahren).
Das Gesenkschmieden hat aufgrund der Erstellung von Gesenken und der erforderlichen Konstruktionsarbeiten zur Herstellung von Arbeitsgesenkkavitäten hohe Anschaffungskosten. Es hat jedoch niedrige wiederkehrende Kosten für jedes Teil, so dass Schmiedeteile mit größerem Produktionsvolumen wirtschaftlicher werden. Dies ist einer der Hauptgründe, warum Gesenkschmiedeteile häufig in der Automobil- und Werkzeugindustrie eingesetzt werden. Ein weiterer Grund, warum Schmiedeteile in diesen Industriezweigen üblich sind, besteht darin, dass Schmiedeteile im Vergleich zu gegossenen oder bearbeiteten Teilen aus demselben Material im Allgemeinen ein um etwa 20 Prozent höheres Festigkeits-Gewichts-Verhältnis aufweisen.
Konstruktion von Gesenkschmiedestücken und Werkzeugbaubearbeiten
Gesenke werden in der Regel aus hochlegiertem oder Werkzeugstahl gefertigt. Die Matrizen müssen schlag- und verschleißfest sein, die Festigkeit bei hohen Temperaturen aufrechterhalten und Zyklen schnellen Aufheizens und Abkühlens standhalten. Um eine bessere, wirtschaftlichere Matrize herzustellen, werden die folgenden Standards eingehalten:
- Die Matrizen teilen sich nach Möglichkeit entlang einer einzigen, flachen Ebene. Wenn nicht, folgt die Trennebene der Kontur des Teils.
- Die Trennfläche ist eine Ebene durch die Mitte des Schmiedens und nicht in der Nähe einer oberen oder unteren Kante.
- Es ist ein ausreichender Tiefgang vorgesehen; normalerweise mindestens 3° für Aluminium und 5° bis 7° für Stahl.
- Großzügige Ausbuchtungen und Radien werden verwendet.
- Rippen sind niedrig und breit.
- Die verschiedenen Abschnitte sind ausgewogen, um extreme Unterschiede im Metallfluss zu vermeiden.
- Faserströmungsleitungen werden voll ausgenutzt.
- Maßtoleranzen sind nicht näher als nötig.
Barrelling tritt auf, wenn sich das Werkstück aufgrund der Reibung zwischen dem Werkstück und der Matrize oder dem Stempel in seiner Mitte so ausbeult, dass es einem Fass ähnelt. Dies führt dazu, dass der zentrale Teil des Werkstücks früher mit den Seiten der Matrize in Kontakt kommt, als wenn keine Reibung vorhanden wäre, wodurch der Druck, der für den Stempel zum Beenden des Schmiedens erforderlich ist, viel stärker ansteigt.
Die Maßtoleranzen eines im Gesenkschmiedeverfahren hergestellten Stahlteils sind in der folgenden Tabelle aufgeführt. Die Abmessungen über die Trennebene werden durch das Schließen der Matrizen beeinflusst und sind daher vom Matrizenverschleiß und der Dicke des Endblitzes abhängig. Abmessungen, die vollständig in einem einzigen Matrizensegment oder einer Hälfte enthalten sind, können mit einer deutlich höheren Genauigkeit beibehalten werden.
Masse | Minus Toleranz | Plus Toleranz |
---|---|---|
0,45 (1) | 0,15 (0,006) | 0,46 (0,018) |
0,91 (2) | 0,20 (0,008) | 0,61 (0,024) |
2,27 (5) | 0,25 (0,010) | 0,76 ( 0,030) |
4,54 (10) | 0.28 (0,011) | 0,84 (0,033) |
9,07 (20) | 0,33 (0,013) | 0,99 (0,039) |
22,68 (50) | 0,48 (0,019) | 1,45 (0,057) |
45,36 (100) | 0,74 (0,029) | 2,21 (0,087) |
Beim Schmieden wird ein Schmiermittel verwendet, um Reibung und Verschleiß zu reduzieren. Es wird auch als Wärmesperre verwendet, um die Wärmeübertragung vom Werkstück auf die Matrize einzuschränken. Schließlich wirkt das Schmiermittel als Trennmittel, um zu verhindern, dass das Teil in den Matrizen haftet.
Pressschmiedearbeiten
Pressschmieden arbeitet durch langsames Aufbringen eines kontinuierlichen Drucks oder einer Kraft, die sich von der nahezu augenblicklichen Wirkung des Fallhammerschmiedens unterscheidet. Die Zeit, die die Matrizen mit dem Werkstück in Kontakt stehen, wird in Sekunden gemessen (im Vergleich zu den Millisekunden von Fallhammerschmieden). Der Pressschmiedevorgang kann entweder kalt oder heiß erfolgen.
Der Hauptvorteil des Pressschmiedens im Vergleich zum Gesenkhammerschmieden ist die Fähigkeit, das gesamte Werkstück zu verformen. Das Fallhammerschmieden verformt normalerweise nur die Oberflächen des Werkstücks, die mit Hammer und Amboss in Kontakt stehen; Das Innere des Werkstücks bleibt relativ unverformt. Ein weiterer Vorteil des Verfahrens ist die Kenntnis der Dehnungsrate des neuen Teils. Durch die Steuerung der Kompressionsrate des Pressschmiedevorgangs kann die innere Dehnung gesteuert werden.
Dieses Verfahren hat einige Nachteile, die meist darauf zurückzuführen sind, dass das Werkstück über einen so langen Zeitraum mit den Matrizen in Kontakt steht. Die Operation ist aufgrund der Anzahl und Länge der Schritte ein zeitaufwendiger Prozess. Das Werkstück kühlt schneller ab, da die Matrizen mit dem Werkstück in Kontakt stehen; Die Matrizen ermöglichen drastisch mehr Wärmeübertragung als die umgebende Atmosphäre. Wenn das Werkstück abkühlt, wird es stärker und weniger duktil, was zu Rissen führen kann, wenn die Verformung anhält. Deshalb werden erhitzte Würfel normalerweise benutzt, um Wärmeverlust zu verringern, Oberflächenfluß zu fördern und die Produktion von feineren Details und von näheren Toleranzen zu ermöglichen. Möglicherweise muss das Werkstück auch erneut erwärmt werden.
Bei hoher Produktivität ist das Pressschmieden wirtschaftlicher als das Hammerschmieden. Die Operation schafft auch engere Toleranzen. Beim Hammerschmieden wird ein Großteil der Arbeit von der Maschine aufgenommen; Beim Pressschmieden wird der größere Prozentsatz der Arbeit im Werkstück verwendet. Ein anderer Vorteil ist, dass die Operation verwendet werden kann, um irgendein Größenteil herzustellen, weil es keine Grenze zur Größe der Pressenschmiedemaschine gibt. Neue Pressschmiedetechniken konnten ein höheres Maß an mechanischer und Orientierungsintegrität schaffen. Durch die Beschränkung der Oxidation auf die äußeren Schichten des Teils treten im fertigen Teil geringere Mikrorisse auf.
Mit dem Pressschmieden können alle Arten von Schmieden durchgeführt werden, einschließlich Frei- und Gegenformschmieden. Pressschmieden erfordert normalerweise weniger Tiefgang als Gesenkschmieden und hat eine bessere Maßgenauigkeit. Außerdem können Pressschmiedeteile häufig in einem Schließen der Matrizen hergestellt werden, was eine einfache Automatisierung ermöglicht.
Upset forgingEdit
Das Stauchschmieden vergrößert den Durchmesser des Werkstücks, indem es seine Länge komprimiert. Basierend auf der Anzahl der produzierten Teile ist dies das am weitesten verbreitete Schmiedeverfahren. Einige Beispiele für gängige Teile, die im Stauchschmiedeverfahren hergestellt werden, sind Motorventile, Kupplungen, Bolzen, Schrauben und andere Befestigungselemente.
Das Stauchschmieden wird normalerweise in speziellen Hochgeschwindigkeitsmaschinen durchgeführt, die als Kurbelpressen bezeichnet werden. Die Maschinen sind in der Regel so eingerichtet, dass sie in der horizontalen Ebene arbeiten, um den schnellen Austausch von Werkstücken von einer Station zur nächsten zu erleichtern, aber das Stauchen kann auch in einer vertikalen Kurbelpresse oder einer hydraulischen Presse erfolgen. Das Anfangswerkstück ist normalerweise Draht oder Stange, aber einige Maschinen können Stangen mit einem Durchmesser von bis zu 25 cm (9,8 Zoll) und einer Kapazität von über 1000 Tonnen aufnehmen. Die Standard-Stauchmaschine verwendet geteilte Matrizen, die mehrere Kavitäten enthalten. Die Matrizen öffnen sich so weit, dass sich das Werkstück von einem Hohlraum zum nächsten bewegen kann; die Matrizen schließen sich dann und das Vortriebswerkzeug oder der Stößel bewegt sich dann in Längsrichtung gegen die Stange und staucht sie in den Hohlraum. Wenn alle Hohlräume in jedem Zyklus genutzt werden, wird mit jedem Zyklus ein fertiges Teil hergestellt, was dieses Verfahren für die Massenproduktion vorteilhaft macht.
Bei der Konstruktion von Teilen, die gestaucht werden sollen, sind folgende Regeln zu beachten:
- Die Länge des nicht getragenen Metalls, das in einem Schlag ohne schädliches Knicken gestaucht werden kann, sollte auf das Dreifache des Stabdurchmessers begrenzt sein.
- Schaftlängen, die größer als das Dreifache des Durchmessers sind, können erfolgreich gestaucht werden, vorausgesetzt, dass der Durchmesser der Verstauchung nicht mehr als das 1,5-fache des Durchmessers des Schafts beträgt.
- In einem Fall, in dem eine Materiallänge von mehr als dem dreifachen des Durchmessers des Materials erforderlich ist und der Durchmesser des Hohlraums nicht mehr als das 1,5-fache des Durchmessers des Materials beträgt, darf die Länge des nicht getragenen Metalls über die Stirnfläche der Matrize hinaus den Durchmesser der Stange nicht überschreiten.
Automatisches Warmschmieden
Beim automatischen Warmschmieden werden Stahlstangen in Mühlenlänge (typischerweise 7 m (23 ft) lang) bei Raumtemperatur in ein Ende der Maschine eingeführt, und am anderen Ende treten warmgeschmiedete Produkte aus. Dies alles geschieht schnell; Kleine Teile können mit einer Geschwindigkeit von 180 Teilen pro Minute (ppm) und größere mit einer Geschwindigkeit von 90 ppm hergestellt werden. Die Teile können fest oder hohl, rund oder symmetrisch, bis zu 6 kg (13 lb) und bis zu 18 cm (7,1 Zoll) im Durchmesser sein. Die Hauptvorteile dieses Prozesses sind seine hohe Produktionsrate und die Fähigkeit, kostengünstige Materialien zu akzeptieren. Es ist wenig Arbeit erforderlich, um die Maschinen zu bedienen.
Es wird kein Blitz erzeugt, so dass die Materialeinsparungen zwischen 20 und 30% gegenüber dem herkömmlichen Schmieden liegen. Das Endprodukt hat eine konstante Temperatur von 1.050 ° C (1.920 ° F), so dass die Luftkühlung zu einem Teil führt, das immer noch leicht bearbeitbar ist (der Vorteil ist das Fehlen von Glühen, das nach dem Schmieden erforderlich ist). Toleranzen sind in der regel ± 0,3mm (0,012 in), oberflächen sind sauber, und entwurf winkel sind 0,5 zu 1 °. Die Standzeit ist fast doppelt so hoch wie beim herkömmlichen Schmieden, da die Kontaktzeiten in der Größenordnung von 0,06 Sekunden liegen. Der Nachteil ist, dass dieser Prozess nur bei kleineren symmetrischen Teilen und Kosten durchführbar ist; Die Anfangsinvestition kann über 10 Millionen US-Dollar betragen, so dass große Mengen erforderlich sind, um diesen Prozess zu rechtfertigen.
Der Prozess beginnt mit der Erwärmung der Stange auf 1.200 bis 1.300 ° C (2.190 bis 2.370 ° F) in weniger als 60 Sekunden mit Hochleistungs-Induktionsspulen. Es wird dann mit Walzen entzundert, zu Rohlingen geschert und durch mehrere aufeinanderfolgende Umformstufen geleitet, in denen es gestaucht, vorgeformt, endgültig geschmiedet und (falls erforderlich) durchstochen wird. Dieser Prozess kann auch mit Hochgeschwindigkeits-Kaltumformvorgängen gekoppelt werden. Im Allgemeinen führt der Kaltumformvorgang die Endbearbeitung durch, so dass die Vorteile der Kaltumformung erzielt werden können, während die hohe Geschwindigkeit des automatischen Warmschmiedens beibehalten wird.
Beispiele für Teile, die mit diesem Verfahren hergestellt werden, sind: Radnabeneinheitslager, Getriebe, Kegelrollenlagerläufe, Edelstahlkopplungsflansche und Halsringe für LP-Gasflaschen. Schaltgetriebe sind ein Beispiel für das automatische Warmschmieden in Verbindung mit der Kaltumformung.
Walzenschmiedearbeiten
Walzenschmieden ist ein Prozess, bei dem Rund- oder Flachstahl in der Dicke reduziert und in der Länge vergrößert wird. Das Walzschmieden wird unter Verwendung von zwei zylindrischen oder halbzylindrischen Walzen durchgeführt, die jeweils eine oder mehrere geformte Nuten enthalten. Ein erhitzter Stab wird in die Rollen eingeführt und wenn er auf eine Stelle trifft, drehen sich die Rollen und der Stab wird progressiv geformt, während er durch die Maschine gerollt wird. Das Stück wird dann auf den nächsten Satz von Nuten übertragen oder umgedreht und wieder in die gleichen Nuten eingesetzt. Dies wird fortgesetzt, bis die gewünschte Form und Größe erreicht ist. Der Vorteil dieses Verfahrens besteht darin, dass es keinen Blitz gibt und dem Werkstück eine günstige Kornstruktur verleiht.
Beispiele für Produkte, die mit dieser Methode hergestellt werden, sind Achsen, Kegelhebel und Blattfedern.
Net-Shape und Near-Net-Shape Schmiedenbearbeiten
Dieser Prozess wird auch als Präzisionsschmieden bezeichnet. Es wurde entwickelt, um Kosten und Abfall im Zusammenhang mit Nachschmiedevorgängen zu minimieren. Deshalb benötigt das Endprodukt von einem Präzisionsschmieden wenig oder keine abschließende maschinelle Bearbeitung. Kosteneinsparungen ergeben sich durch den Einsatz von weniger Material und damit weniger Ausschuss, die Gesamtabnahme des Energieverbrauchs und die Reduzierung oder Eliminierung der Bearbeitung. Präzisionsschmieden erfordert auch weniger Entwurf, 1° bis 0°. Der Nachteil dieses Prozesses sind seine Kosten, daher wird es nur implementiert, wenn eine signifikante Kostensenkung erreicht werden kann.
Kaltschmieden
Near Net Shape Schmieden ist am häufigsten, wenn Teile geschmiedet werden, ohne die Schnecke, Stange oder Billet zu erhitzen. Aluminium ist ein allgemeines Material, das abhängig von abschließender Form kalt geschmiedet sein kann. Die Schmierung der zu formenden Teile ist entscheidend, um die Lebensdauer der Gegenwerkzeuge zu erhöhen.
Induktionsschmiedebearbeiten
Im Gegensatz zu den oben genannten Verfahren basiert das Induktionsschmieden auf der Art des verwendeten Heizstils. Viele der oben genannten Verfahren können in Verbindung mit dieser Heizmethode verwendet werden.
Multidirektionales Schmieden
Multidirektionales Schmieden ist das Formen eines Werkstücks in einem einzigen Schritt in mehrere Richtungen. Die multidirektionale Umformung erfolgt durch konstruktive Maßnahmen des Werkzeugs. Die vertikale Bewegung des Pressenstößels wird mit Keilen umgeleitet, die die Kraft der Schmiedepresse in horizontale Richtungen verteilen und umleiten.
Isothermes Schmieden
Isothermes Schmieden ist ein Prozess, bei dem die Materialien und die Matrize auf die gleiche Temperatur erhitzt werden (iso- Bedeutung „gleich“). Adiabatische Erwärmung wird verwendet, um die Verformung des Materials zu unterstützen, was bedeutet, dass die Dehnungsraten stark kontrolliert werden. Wird häufig zum Schmieden von Aluminium verwendet, das eine niedrigere Schmiedetemperatur als Stähle aufweist. Schmiedetemperaturen für Aluminium sind um 430 °C (806 °F), während Stähle und Superlegierungen 930 bis 1.260 °C (1.710 bis 2.300 °F) sein können.
Vorteile:
- Netznahe Formen, die zu geringeren Bearbeitungsanforderungen und damit geringeren Ausschussraten führen
- Reproduzierbarkeit des Teils
- Aufgrund des geringeren Wärmeverlusts können kleinere Maschinen zum Schmieden verwendet werden
Nachteile:
- Höhere Werkzeugmaterialkosten für Temperaturen und Drücke
- Es sind gleichmäßige Heizsysteme erforderlich
- Schutzatmosphären oder Vakuum, um die Oxidation der Werkzeuge und des Materials zu reduzieren
- Niedrige Produktionsraten
Leave a Reply