Forgeage

Il existe de nombreux types de procédés de forgeage disponibles; cependant, ils peuvent être regroupés en trois classes principales :
- Étiré: la longueur augmente, la section diminue
- Bouleversé: la longueur diminue, la section augmente
- Pressé dans des matrices de compression fermées: produit un flux multidirectionnel
Les processus de forgeage courants incluent: forgeage par rouleaux, emboutissage, emboutissage, forgeage à matrice ouverte, forgeage par empreinte (forgeage à matrice étroite), forgeage par presse, forgeage à froid forgeage à chaud automatique et bouleversement.
Temperaturedit
Tous les procédés de forgeage suivants peuvent être effectués à différentes températures; cependant, ils sont généralement classés selon que la température du métal est supérieure ou inférieure à la température de recristallisation. Si la température est supérieure à la température de recristallisation du matériau, il est considéré comme un forgeage à chaud; si la température est inférieure à la température de recristallisation du matériau mais supérieure à 30% de la température de recristallisation (sur une échelle absolue), il est considéré comme un forgeage à chaud; s’il est inférieur à 30% de la température de recristallisation (généralement la température ambiante), il est considéré comme un forgeage à froid. Le principal avantage du forgeage à chaud est qu’il peut être fait plus rapidement et plus précisément, et que le métal est déformé, les effets de durcissement sont annulés par le processus de recristallisation. Le forgeage à froid entraîne généralement un durcissement de la pièce.
Drop forgingEdit
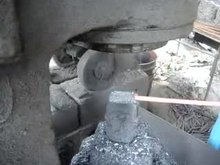
Play media
Le forgeage par goutte est un processus de forgeage où un marteau est soulevé puis « déposé » sur la pièce à usiner pour la déformer en fonction de la forme de la matrice. Il existe deux types de forgeage par goutte: le forgeage par goutte à matrice ouverte et le forgeage par goutte à empreinte (ou à matrice fermée). Comme les noms l’indiquent, la différence réside dans la forme de la matrice, la première n’entourant pas complètement la pièce, tandis que la seconde le fait.
Forgeage par goutte à matrice ouverte


Le forgeage à matrice ouverte est également connu sous le nom de forgeage de smith. Dans le forgeage à matrice ouverte, un marteau frappe et déforme la pièce, qui est placée sur une enclume fixe. Le forgeage à matrice ouverte tire son nom du fait que les matrices (les surfaces en contact avec la pièce) n’entourent pas la pièce, ce qui lui permet de s’écouler sauf lorsqu’elles sont en contact avec les matrices. L’opérateur doit donc orienter et positionner la pièce pour obtenir la forme souhaitée. Les matrices sont généralement de forme plate, mais certaines ont une surface spécialement formée pour des opérations spécialisées. Par exemple, une matrice peut avoir une surface ronde, concave ou convexe ou être un outil pour former des trous ou être un outil de coupure.Les pièces forgées à matrice ouverte peuvent être travaillées en formes comprenant des disques, des moyeux, des blocs, des arbres (y compris des arbres étagés ou avec des brides), des manchons, des cylindres, des méplats, des hexagones, des ronds, des plaques et certaines formes personnalisées.Le forgeage à matrice ouverte se prête à de courts tirages et convient à la forge d’art et au travail sur mesure. Dans certains cas, le forgeage à matrice ouverte peut être utilisé pour ébaucher des lingots pour les préparer à des opérations ultérieures. Le forgeage à matrice ouverte peut également orienter le grain pour augmenter la résistance dans la direction requise.
Avantages du forgeage à matrice ouverte
- Réduction des risques de vides
- Meilleure résistance à la fatigue
- microstructure améliorée
- Écoulement continu des grains
- Granulométrie plus fine
- Plus grande résistance
- Meilleure réponse au traitement thermique
- Amélioration de la qualité interne
- Plus grande fiabilité des propriétés mécaniques, de la ductilité et de la résistance aux chocs
Le « cogging » est la déformation successive d’une barre sur sa longueur à l’aide d’une forge de goutte à matrice ouverte. Il est couramment utilisé pour travailler un morceau de matière première à la bonne épaisseur. Une fois que l’épaisseur appropriée est atteinte, la largeur appropriée est obtenue par « bordure ».La « bordure » est le processus de concentration du matériau à l’aide d’une matrice ouverte de forme concave. Le processus est appelé « bordure » car il est généralement effectué aux extrémités de la pièce. Le « fullering » est un processus similaire qui amincit les sections du forgeage à l’aide d’une matrice de forme convexe. Ces processus préparent les pièces à usiner pour d’autres processus de forgeage.
-
Bordure
-
Fullering
Forgeage à empreinte
Le forgeage à empreinte est également appelé « forgeage à matrice fermée ». Dans le forgeage par empreinte, le métal est placé dans une matrice ressemblant à un moule, qui est fixée à une enclume. Habituellement, la matrice de marteau est également en forme. Le marteau est ensuite déposé sur la pièce, provoquant l’écoulement du métal et le remplissage des cavités de la matrice. Le marteau est généralement en contact avec la pièce à l’échelle de la milliseconde. Selon la taille et la complexité de la pièce, le marteau peut être lâché plusieurs fois de suite rapidement. L’excès de métal est extrait des cavités de la matrice, formant ce qu’on appelle un « flash ». Le flash se refroidit plus rapidement que le reste du matériau; ce métal froid est plus résistant que le métal de la matrice, ce qui aide à empêcher la formation de plus de flash. Cela oblige également le métal à remplir complètement la cavité de la matrice. Après le forgeage, le flash est retiré.
Dans le forgeage commercial de matrices d’impression, la pièce est généralement déplacée à travers une série de cavités dans une matrice pour passer d’un lingot à la forme finale. La première impression est utilisée pour répartir le métal dans la forme rugueuse en fonction des besoins des cavités ultérieures; cette impression est appelée impression de « bordure », de « fuller » ou de « flexion ». Les cavités suivantes sont appelées cavités de « blocage », dans lesquelles la pièce travaille dans une forme qui ressemble plus au produit final. Ces étapes confèrent généralement à la pièce des coudes généreux et de gros filets. La forme finale est forgée dans une cavité d’empreinte « finale » ou « finisseur ». S’il n’y a qu’un petit nombre de pièces à faire, il peut être plus économique pour la matrice de ne pas avoir de cavité d’empreinte finale et d’usiner les caractéristiques finales.
Le forgeage par empreinte a été amélioré ces dernières années grâce à une automatisation accrue qui comprend le chauffage par induction, l’alimentation mécanique, le positionnement et la manipulation, ainsi que le traitement thermique direct des pièces après le forgeage.Une variante du forgeage par empreinte est appelée « forgeage sans flash » ou « véritable forgeage à matrice fermée ». Dans ce type de forgeage, les cavités de la matrice sont complètement fermées, ce qui empêche la pièce de former un éclair. L’avantage majeur de ce processus est que moins de métal est perdu au flash. Le flash peut représenter 20 à 45% du matériau de départ. Les inconvénients de ce processus incluent un coût supplémentaire dû à une conception de matrice plus complexe et à la nécessité d’une meilleure lubrification et d’un meilleur placement de la pièce.
Il existe d’autres variantes de formation de pièces qui intègrent le forgeage par empreinte. Une méthode consiste à couler une préforme de forgeage à partir de métal liquide. La coulée est retirée après sa solidification, mais encore chaude. Il est ensuite terminé dans une matrice à cavité unique. Le flash est coupé, puis la pièce est trempée. Une autre variante suit le même procédé que décrit ci-dessus, sauf que la préforme est produite par dépôt par pulvérisation de gouttelettes métalliques dans des collecteurs en forme (similaire au procédé Osprey).
Le forgeage à matrice fermée a un coût initial élevé en raison de la création de matrices et des travaux de conception nécessaires pour créer des cavités de matrices de travail. Cependant, il a de faibles coûts récurrents pour chaque pièce, ainsi les pièces forgées deviennent plus économiques avec un plus grand volume de production. C’est l’une des principales raisons pour lesquelles les pièces forgées à matrice fermée sont souvent utilisées dans les industries de l’automobile et de l’outillage. Une autre raison pour laquelle les pièces forgées sont courantes dans ces secteurs industriels est que les pièces forgées ont généralement un rapport résistance / poids supérieur d’environ 20% par rapport aux pièces moulées ou usinées du même matériau.
Conception de pièces forgées et d’outillagesmodifier
Les matrices de forgeage sont généralement en acier fortement allié ou à outils. Les matrices doivent être résistantes aux chocs et à l’usure, maintenir leur résistance à des températures élevées, résister à des cycles de chauffage et de refroidissement rapides. Afin de produire une filière meilleure et plus économique, les normes suivantes sont maintenues:
- La filière part le long d’un seul plan plat dans la mesure du possible. Sinon, le plan de séparation suit le contour de la pièce.
- La surface de séparation est un plan passant par le centre du forgeage et non près d’un bord supérieur ou inférieur.
- Un tirant d’eau adéquat est fourni; généralement au moins 3 ° pour l’aluminium et 5 ° à 7 ° pour l’acier.
- Des filets et des rayons généreux sont utilisés.Les côtes sont basses et larges.
- Les différentes sections sont équilibrées pour éviter une différence extrême dans le flux de métal.
- On tire pleinement parti des lignes de flux de fibres.
- Les tolérances dimensionnelles ne sont pas plus proches que nécessaire.
Le barillet se produit lorsque, en raison du frottement entre la pièce à usiner et la matrice ou le poinçon, la pièce à usiner se gonfle en son centre de manière à ressembler à un barillet. Cela conduit la partie centrale de la pièce à travailler à venir en contact avec les côtés de la matrice plus tôt que s’il n’y avait pas de frottement présent, créant une augmentation beaucoup plus importante de la pression requise pour que le poinçon termine le forgeage.
Les tolérances dimensionnelles d’une pièce en acier produite selon la méthode de forgeage par empreinte sont décrites dans le tableau ci-dessous. Les dimensions à travers le plan de séparation sont affectées par la fermeture des matrices, et dépendent donc de l’usure de la matrice et de l’épaisseur du flash final. Les dimensions qui sont entièrement contenues dans un seul segment de matrice ou une moitié peuvent être maintenues à un niveau de précision nettement supérieur.
Masse | Tolérance moins | Tolérance plus |
---|---|---|
0,45(1) | 0,15( 0,006) | 0,46(0,018) |
0,91(2) | 0,20 (0,008) | 0,61 (0,024) |
2,27(5) | 0,25 (0,010) | 0,76 (0,030) |
4,54(10) | 0.28 (0,011) | 0,84 (0,033) |
9,07(20) | 0,33 (0,013) | 0,99 (0,039) |
22,68 (50) | 0,48 (0,019) | 1,45(0,057) |
45,36(100) | 0,74(0,029) | 2,21(0,087) |
Un lubrifiant est utilisé lors du forgeage pour réduire les frottements et l’usure. Il est également utilisé comme barrière thermique pour limiter le transfert de chaleur de la pièce à usiner à la matrice. Enfin, le lubrifiant agit comme un composé de séparation pour empêcher la pièce de coller dans les matrices.
Forgeage à la pressedit
Le forgeage à la presse fonctionne en appliquant lentement une pression ou une force continue, qui diffère de l’impact quasi instantané du forgeage au marteau. La durée pendant laquelle les matrices sont en contact avec la pièce à usiner est mesurée en secondes (par rapport aux millisecondes des forges à marteau-piqueur). L’opération de forgeage par presse peut être effectuée à froid ou à chaud.
Le principal avantage du forgeage par presse, par rapport au forgeage au marteau, est sa capacité à déformer la pièce complète. Le forgeage au marteau ne déforme généralement que les surfaces de la pièce en contact avec le marteau et l’enclume; l’intérieur de la pièce restera relativement non déformé. Un autre avantage du procédé est la connaissance de la vitesse de déformation de la nouvelle pièce. En contrôlant le taux de compression de l’opération de forgeage de la presse, la déformation interne peut être contrôlée.
Il y a quelques inconvénients à ce procédé, la plupart provenant du fait que la pièce est en contact avec les matrices pendant une période de temps aussi longue. L’opération est un processus fastidieux en raison de la quantité et de la longueur des étapes. La pièce à usiner se refroidira plus rapidement car les matrices sont en contact avec la pièce à usiner; les matrices facilitent considérablement plus le transfert de chaleur que l’atmosphère environnante. Au fur et à mesure que la pièce se refroidit, elle devient plus résistante et moins ductile, ce qui peut induire une fissuration si la déformation se poursuit. Par conséquent, les matrices chauffées sont généralement utilisées pour réduire les pertes de chaleur, favoriser l’écoulement de la surface et permettre la production de détails plus fins et de tolérances plus étroites. La pièce peut également devoir être réchauffée.
Lorsqu’il est fait avec une productivité élevée, le forgeage à la presse est plus économique que le forgeage au marteau. L’opération crée également des tolérances plus étroites. Dans le forgeage au marteau, une grande partie du travail est absorbée par la machine; dans le forgeage à la presse, le pourcentage de travail le plus élevé est utilisé dans la pièce à usiner. Un autre avantage est que l’opération peut être utilisée pour créer n’importe quelle pièce de taille car il n’y a pas de limite à la taille de la machine de forgeage par presse. Les nouvelles techniques de forgeage à la presse ont permis de créer un degré plus élevé d’intégrité mécanique et d’orientation. Par la contrainte d’oxydation sur les couches externes de la pièce, des niveaux réduits de microfissure se produisent dans la pièce finie.
Le forgeage à la presse peut être utilisé pour effectuer tous les types de forgeage, y compris le forgeage à matrice ouverte et le forgeage à empreinte. Le forgeage par presse à empreinte nécessite généralement moins de tirage que le forgeage par goutte et a une meilleure précision dimensionnelle. De plus, les pièces forgées à la presse peuvent souvent être réalisées en une seule fermeture des matrices, ce qui permet une automatisation facile.
Upset forgingEdit
Le forgeage bouleversé augmente le diamètre de la pièce en comprimant sa longueur. Basé sur le nombre de pièces produites, c’est le processus de forgeage le plus utilisé. Quelques exemples de pièces communes produites à l’aide du processus de forgeage bouleversé sont les soupapes de moteur, les accouplements, les boulons, les vis et autres fixations.
Le forgeage bouleversé est généralement effectué dans des machines spéciales à grande vitesse appelées presses à manivelle. Les machines sont généralement configurées pour travailler dans le plan horizontal, afin de faciliter l’échange rapide des pièces d’une station à l’autre, mais le bouleversement peut également être effectué dans une presse à manivelle verticale ou une presse hydraulique. La pièce initiale est généralement du fil ou une tige, mais certaines machines peuvent accepter des barres d’un diamètre allant jusqu’à 25 cm (9,8 po) et d’une capacité de plus de 1 000 tonnes. La machine de refoulement standard utilise des matrices fendues contenant plusieurs cavités. Les matrices s’ouvrent suffisamment pour permettre à la pièce de passer d’une cavité à l’autre; les matrices se ferment alors et l’outil de captage, ou vérin, se déplace alors longitudinalement contre la barre, la faisant basculer dans la cavité. Si toutes les cavités sont utilisées à chaque cycle, une pièce finie sera produite à chaque cycle, ce qui rend ce processus avantageux pour la production en série.
Ces règles doivent être suivies lors de la conception de pièces à forger:
- La longueur du métal non supporté qui peut être bouleversé en un coup sans flambage préjudiciable doit être limitée à trois fois le diamètre de la barre.
- Des longueurs de stock supérieures à trois fois le diamètre peuvent être bouleversées avec succès, à condition que le diamètre du bouleversement ne dépasse pas 1,5 fois le diamètre du stock.
- Dans un bouleversement nécessitant une longueur de crosse supérieure à trois fois le diamètre de la crosse, et où le diamètre de la cavité ne dépasse pas 1,5 fois le diamètre de la crosse, la longueur du métal non supporté au-delà de la face de la matrice ne doit pas dépasser le diamètre de la barre.
Forgeage à chaud automatique
Le processus de forgeage à chaud automatique consiste à introduire des barres d’acier de longueur de fraise (généralement de 7 m (23 pi) de long) dans une extrémité de la machine à température ambiante et des produits forgés à chaud émergent de l’autre extrémité. Tout cela se produit rapidement; de petites pièces peuvent être fabriquées à raison de 180 parties par minute (ppm) et de plus grandes peuvent être fabriquées à raison de 90 ppm. Les pièces peuvent être pleines ou creuses, rondes ou symétriques, jusqu’à 6 kg (13 lb) et jusqu’à 18 cm (7,1 po) de diamètre. Les principaux avantages de ce processus sont son taux de production élevé et sa capacité à accepter des matériaux à faible coût. Peu de travail est nécessaire pour faire fonctionner la machine.
Il n’y a pas de flash produit, donc les économies de matière sont comprises entre 20 et 30% par rapport au forgeage conventionnel. Le produit final est à une température constante de 1 050 ° C (1 920 ° F), de sorte que le refroidissement par air donnera une pièce encore facilement usinable (l’avantage étant le manque de recuit requis après le forgeage). Les tolérances sont généralement de ± 0,3 mm (0,012 po), les surfaces sont propres et les angles de tirage sont de 0,5 à 1 °. La durée de vie de l’outil est presque le double de celle du forgeage conventionnel car les temps de contact sont de l’ordre de 0,06 seconde. L’inconvénient est que ce processus n’est réalisable que sur des pièces symétriques et des coûts plus petits; l’investissement initial peut dépasser 10 millions de dollars, de sorte que de grandes quantités sont nécessaires pour justifier ce processus.
Le processus commence par chauffer la barre à 1 200 à 1 300 ° C (2 190 à 2 370 °F) en moins de 60 secondes à l’aide de bobines d’induction haute puissance. Il est ensuite détartré à l’aide de rouleaux, cisaillé en ébauches, et transféré par plusieurs étapes de formage successives, au cours desquelles il est bouleversé, préformé, définitivement forgé et percé (si nécessaire). Ce procédé peut également être couplé à des opérations de formage à froid à grande vitesse. Généralement, l’opération de formage à froid fera l’étape de finition de sorte que les avantages du travail à froid peuvent être obtenus, tout en maintenant la grande vitesse du forgeage automatique à chaud.
Des exemples de pièces fabriquées par ce procédé sont: roulements de moyeu de roue, engrenages de transmission, bagues de roulement à rouleaux coniques, brides d’accouplement en acier inoxydable et bagues de col pour bouteilles de gaz LP. Les engrenages à transmission manuelle sont un exemple de forgeage automatique à chaud utilisé en conjonction avec le travail à froid.
Forgeage en laminagEdit
Le forgeage en rouleaux est un processus dans lequel les barres rondes ou plates sont réduites en épaisseur et augmentées en longueur. Le forgeage en rouleaux est effectué à l’aide de deux rouleaux cylindriques ou semi-cylindriques contenant chacun une ou plusieurs rainures profilées. Une barre chauffée est insérée dans les rouleaux et lorsqu’elle frappe un endroit, les rouleaux tournent et la barre est progressivement façonnée au fur et à mesure qu’elle est roulée à travers la machine. La pièce est ensuite transférée dans le jeu de rainures suivant ou retournée et réinsérée dans les mêmes rainures. Cela continue jusqu’à ce que la forme et la taille souhaitées soient atteintes. L’avantage de ce procédé est qu’il n’y a pas de flash et qu’il confère une structure de grain favorable à la pièce.
Des exemples de produits fabriqués selon cette méthode comprennent des essieux, des leviers coniques et des ressorts à lames.
Forgeage en forme de filet et en forme de quasi-filet
Ce processus est également connu sous le nom de forgeage de précision. Il a été développé pour minimiser les coûts et les déchets associés aux opérations de post-forgeage. Par conséquent, le produit final d’un forgeage de précision nécessite peu ou pas d’usinage final. Des économies de coûts sont obtenues grâce à l’utilisation de moins de matériaux, et donc de moins de déchets, à la diminution globale de l’énergie utilisée et à la réduction ou à l’élimination de l’usinage. Le forgeage de précision nécessite également moins d’ébauche, de 1° à 0°. L’inconvénient de ce processus est son coût, il n’est donc mis en œuvre que si une réduction significative des coûts peut être réalisée.
Forgeage à froid
Le forgeage en forme de filet est le plus courant lorsque des pièces sont forgées sans chauffer la limace, la barre ou la billette. L’aluminium est un matériau courant qui peut être forgé à froid en fonction de la forme finale. La lubrification des pièces en cours de formation est essentielle pour augmenter la durée de vie des matrices d’accouplement.
Forgeage par induction
Contrairement aux procédés ci-dessus, le forgeage par induction est basé sur le type de style de chauffage utilisé. Un grand nombre des processus ci-dessus peuvent être utilisés en conjonction avec cette méthode de chauffage.
Forgeage multidirectionnel
Le forgeage multidirectionnel consiste à former une pièce à usiner en une seule étape dans plusieurs directions. Le formage multidirectionnel se fait par des mesures constructives de l’outil. Le mouvement vertical du vérin de la presse est redirigé à l’aide de cales qui répartissent et redirigent la force de la presse à forger dans des directions horizontales.
Forgeage isothermedit
Le forgeage isotherme est un processus par lequel les matériaux et la matrice sont chauffés à la même température (iso – ce qui signifie « égal »). Le chauffage adiabatique est utilisé pour aider à la déformation du matériau, ce qui signifie que les taux de déformation sont hautement contrôlés. Couramment utilisé pour forger l’aluminium, qui a une température de forgeage inférieure à celle des aciers. Les températures de forgeage de l’aluminium sont d’environ 430 ° C (806 ° F), tandis que les aciers et les superalliages peuvent être de 930 à 1 260 ° C (1 710 à 2 300 ° F).
Avantages:
- Des formes proches du filet qui entraînent des exigences d’usinage plus faibles et donc des taux de rebut plus faibles
- Reproductibilité de la pièce
- En raison de la perte de chaleur plus faible, des machines plus petites peuvent être utilisées pour fabriquer le forgeage
Inconvénients:
- Des coûts de matériau de matrice plus élevés pour gérer les températures et les pressions
- Des systèmes de chauffage uniformes sont nécessaires
- Des atmosphères protectrices ou du vide pour réduire l’oxydation des matrices et du matériau
- Faibles taux de production
Leave a Reply