鍛造

利用可能な鍛造プロセスの多くの異なる種類があります;しかし、彼らは三つの主要なクラスにグループ化することができます。
- 引き出し:長さが増加し、断面が減少します
- 動揺:長さが減少し、断面が増加します
- 閉じた圧縮金型に絞ら:多方向の流れを生成します
一般的な鍛造: ロール鍛造、スウェージング、コギング、オープンダイ鍛造、インプレッションダイ鍛造(クローズダイ鍛造)、プレス鍛造、冷間鍛造自動熱間鍛造、動揺。
TemperatureEdit
以下の鍛造プロセスはすべて、さまざまな温度で行うことができますが、一般的に金属温度が再結晶温度 温度が材料の再結晶化の温度の上にあればそれは熱い鍛造材とみなされます; 温度が材料の再結晶温度を下回っているが、再結晶温度の30%を超える(絶対スケールで)場合、それは温鍛造とみなされ、再結晶温度(通常は室温)の30%を下回 熱間鍛造の主な利点は、より迅速かつ正確に行うことができ、金属が変形するにつれて加工硬化効果が再結晶プロセスによって否定されることで 冷たい鍛造材は部分の加工硬化で普通起因します。
ドロップforgingEdit
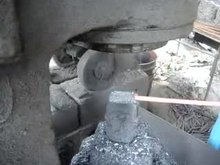
Play media
ドロップ鍛造は、ハンマーを上げてから、金型の形状に応じて変形させるためにワークに”落とし” ドロップ鍛造には、オープンダイドロップ鍛造とインプレッションダイ(またはクローズドダイ)ドロップ鍛造の2つのタイプがあります。 名前が意味するように、違いは金型の形状にあり、前者はワークピースを完全に囲んでいないが、後者はそうである。
オープンダイドロップ鍛造




オープンダイ鍛造はまた、スミス鍛造として知られています。 オープンダイス鍛造では、ハンマーが打ち、固定金敷の上に置かれる工作物を変形させる。 オープン型鍛造は、金型(ワークと接触している表面)がワークを囲まないという事実からその名前を得て、金型に接触した場所を除いて流れることができます。 従ってオペレータは望ましい形を得るために工作物を方向づけ、置く必要がある。 金型は、通常、形状が平坦であるが、いくつかは、特殊な操作のための特別な形状の表面を有しています。 例えば、ダイは、円形、凹状、または凸状の表面を有してもよく、または穴を形成するための工具であってもよく、またはカットオフ工具であってもよい。オープンダイスの鍛造材はディスク、ハブ、ブロック、シャフト(を含むステップシャフトまたはフランジと)、袖、シリンダー、平たい箱、hexes、円形、版およびある注文の形を含んでいる形に働かせることができます。オープンダイスの鍛造材は短い操業にそれ自身を貸し、芸術のsmithingおよび注文の仕事のために適切である。 場合によっては、その後の作業のためにそれらを準備するために、粗形状のインゴットに開放型鍛造を採用することができる。 オープンダイス鍛造はまた必須の方向の強さを高めるために穀物を方向づけるかもしれません。
オープンダイ鍛造の利点
- ボイドの減少チャンス
- より良い疲労抵抗
- 改善された微細構造
- 連続粒流
- より微細な粒径
- より大きな強さ
- 熱処理へのより良い応答
- 内部品質の改善
- 機械的性質、延性および耐衝撃性のより高い信頼性
“コギング”は、オープンダイドロップフォージを使用して、その長さに沿ってバーの連続変形です。 それは一般的適切な厚さに原料の部分を働かせるためにです。 適切な厚さが達成されれば適切な幅は”エッジング”によって達成される。”エッジング”とは、凹形のオープンダイを使用して材料を集中させるプロセスです。 このプロセスは、通常、ワークピースの端部で実行されるため、”エッジング”と呼ばれます。 “Fullering”は凸の定形ダイスを使用して鍛造材のセクションを薄くする同じようなプロセスである。 これらのプロセスはそれ以上の鍛造材プロセスのために工作物を準備する。p>
フラー
フラー
フラー
インプレッションダイ鍛造
インプレッションダイ鍛造は、”クローズドダイ鍛造”とも呼ばれます。 印象型鍛造では、金敷に取り付けられた金型に似た金型に金属を入れます。 通常、ハンマーは同様に形づけられます死にます。 ハンマーは工作物でそれから落ちま、金属を流れ、ダイスキャビティを満たします。 ハンマーはミリ秒のスケールの工作物と接触して一般にあります。 部品のサイズと複雑さに応じて、ハンマーは連続して複数回落とされることがあります。 余分な金属がダイキャビティから絞り出され、”フラッシュ”と呼ばれるものが形成されます。 フラッシュは材料の残りより急速に冷却します;この涼しい金属はダイスの金属より強いです、従ってより多くのフラッシュが形作ることを防ぐ これはまた、金属がダイキャビティを完全に満たすように強制する。 鍛造後、フラッシュは除去される。
商業的な印象ダイ鍛造では、ワークピースは通常、インゴットから最終的な形状に到達するためにダイ内の一連の空洞を通って移動されます。 第一印象がより遅いキャビティの必要性に調和の荒い形に金属を配るのに使用されています;この印象は”エッジング”、”fullering”、または”曲がる”印象と呼ばれます。 以下の空洞は、作品がより密接に最終製品に似た形状に働いている”ブロッキング”空洞と呼ばれています。 これらの段階は通常寛大なくねりおよび大きい切り身が付いている工作物を与える。 最終的な形は”最終的な”か”フィニッシャー”の印象キャビティで造られる。 行われる部品の短い実行だけがある場合は、金型が最終的な印象キャビティを欠いており、代わりに最終的な機能を機械化することがより経済的で
印象型鍛造は、誘導加熱、機械的供給、位置決めおよび操作、および鍛造後の部品の直接熱処理を含む自動化の増加により、近年改善されている。印象型鍛造のバリエーションの一つは、”フラッシュレス鍛造”、または”真のクローズドダイ鍛造”と呼ばれています。 このタイプの鍛造材では、ダイスキャビティはフラッシュの形成からの工作物を保つ完全に閉鎖しています。 このプロセスへの主な利点はより少ない金属が点滅するために失われることである。 フラッシュは出発材料の20から45%を占めることができます。 このプロセスの欠点には、より複雑なダイ設計による追加コストと、より優れた潤滑およびワーク配置の必要性が含まれます。
印象型鍛造を統合する部品形成の他のバリエーションがあります。 一つの方法は、液体金属から鍛造プリフォームを鋳造することを組み込んでいます。 鋳造は凝固した後、まだ熱い間に除去される。 それは単一キャビティで死にますそれから終わります。 フラッシュは整えられます、そして部品は堅くなります癒やしますあります。 別の変形は、プリフォームが成形されたコレクターへの金属液滴の噴霧堆積によって製造されることを除いて、上記で概説したのと同じプロセスに従う(オスプレイプロセスに類似している)。
クローズドダイ鍛造は、金型の作成と加工金型キャビティを作るための設計作業が必要なため、初期コストが高くなります。 但し、それに各部分のための低い定期的な費用があります、従って鍛造材はより大きい生産の容積とより経済的になります。 これは、自動車および工具産業で閉鎖型鍛造品が頻繁に使用される主な理由の1つです。 これらの産業分野で鍛造品が一般的であるもう一つの理由は、鍛造品が一般に、同じ材料の鋳造または機械加工部品と比較して約20%高い強度対重量比
印象ダイス鍛造材およびtoolingEditの設計
鍛造材ダイスは通常高合金か工具鋼から成っています。 金型は耐衝撃性と耐摩耗性があり、高温で強度を維持し、急速な加熱と冷却のサイクルに耐える能力を持っていなければなりません。 よりよく、より経済的の作り出すためには次の標準は維持されます死にます:
- 単一の、平面に沿うダイスの部品可能な限り。 そうでない場合、パーティングプレーンは部品の輪郭に従います。
- パーティング面は、鍛造の中心を通る平面であり、上端または下端の近くではありません。
- 十分な草案は提供されます;通常アルミニウムのための少なくとも3°および鋼鉄のための5°から7°。
- 寛大なフィレと半径が使用されます。
- リブは低く、広いです。
- 様々なセクションは、金属の流れの極端な違いを避けるためにバランスが取れています。
- 繊維の流れラインの十分な利点は取られます。
- 寸法公差は必要以上に近いものではありません。
バレルは、ワークピースとダイまたはパンチとの間の摩擦により、ワークピースがバレルに似ているように中央で膨らみます。 これは鍛造材を終える穿孔器に必要な圧力の大いにより大きい増加を作成する摩擦がなかったらダイスの側面と接触するために仕事の部分の中央部を早くよりもたらします。
印象型鍛造法を用いて製造された鋼部品の寸法公差を以下の表に概説します。 従って分割の平面を渡る次元はダイスの閉鎖によって影響され、最終的なフラッシュのダイスの摩耗そして厚さに依存しています。 単一のダイスの区分または半分の内で完全に含まれている次元は正確さのかなりより大きいレベルで維持することができる。
質量 | マイナス公差 | プラス公差 | |||||||||
---|---|---|---|---|---|---|---|---|---|---|---|
0.45(1) | 0.15(0.006) | ||||||||||
0.91(2) | 0.20(0.008) | 0.61(0.024) | |||||||||
2.27(5) | 0.25(0.010) | 0.76(5) | 0.76(5) | 0.76(5) | 0.76(5) | 0.76(5) | 0.76(5) | 0.76(5) | 0.76(5) | 0.76(5) | 0.76(5)0.030) |
4.54(10) | 0.030) | ||||||||||
4.54(10) | 0.03028(0.011) | 0.84(0.033) | |||||||||
9.07(20) | 0.33(0.013) | 0.99(0.039) | |||||||||
22.68(50) | 0.48(0.019)1.45(0.057) | ||||||||||
45.36(100) | 0.74(0.029) | 2.21(0.087) |
摩擦や摩耗を軽減するために鍛造するときに潤滑剤が使用されます。 また熱障壁として工作物からのダイスへの熱伝達を制限することを使用します。 最後に、潤滑剤は部品がダイスで付くことを防ぐために分割の混合物として機能します。
プレス鍛造編集
プレス鍛造は、ドロップハンマー鍛造の瞬間的な衝撃とは異なる連続的な圧力または力をゆっくりと加えることによっ ダイスが工作物と接触してある時間は秒単位で測定される(低下ハンマーの鍛造物のミリ秒と比較して)。 出版物の鍛造材操作は冷たいですか熱いすることができます。プレス鍛造の主な利点は、ドロップハンマー鍛造と比較して、完全なワークピースを変形させる能力です。
プレス鍛造の主な利点は、ドロップハンマー鍛造 低下ハンマーの鍛造材は通常ハンマーおよび金敷と接触して仕事の部分の表面だけを変形させます;工作物の内部は比較的undeformedとどまります。 プロセスへのもう一つの利点は新しい部品の緊張率の知識を含んでいる。 プレス鍛造動作の圧縮速度を制御することにより、内部ひずみを制御することができる。
このプロセスにはいくつかの欠点があり、そのほとんどはワークがこのような長期間ダイと接触していることに起因します。
このプロセスには この操作は、ステップの量と長さのために時間のかかるプロセスです。 工作物はダイスが工作物と接触してあるのでより速く冷却します;ダイスは周囲の大気より徹底的により多くの熱伝達を促進します。 工作物が冷却すると同時に変形が続ければ割れることを引き起こすかもしれないより強く、より少なく延性があるようになります。 従って、熱されたダイスが通常損失熱を減らし、表面の流れを促進し、より良い細部およびより近い許容の生産を可能にするのに使用されています。 工作物はまた再加熱される必要があるかもしれません。
高い生産性で行われた場合、プレス鍛造はハンマー鍛造よりも経済的です。 また、この操作により、より近い許容誤差が作成されます。 ハンマーの鍛造材で多くの仕事は機械類によって吸収されます;出版物の鍛造材で、仕事のより大きいパーセントが仕事の部分で使用される時。 もう一つの利点は出版物の鍛造材機械のサイズへ限界がないので操作がサイズの部品を作成するのに使用することができることである。 新しい出版物の鍛造材の技術は機械およびオリエンテーションの完全性の高度を作成できました。 部品の外の層への酸化の抑制によって、microcrackingの減らされたレベルは終了する部品に起こります。プレス鍛造は、オープンダイおよびインプレッションダイ鍛造を含むすべてのタイプの鍛造を行うために使用することができます。
プレス鍛造は、 インプレスダイプレス鍛造は、通常、ドロップ鍛造よりもドラフトが少なく、寸法精度が優れています。 また、プレス鍛造は、多くの場合、金型の一つの閉鎖で行うことができ、容易な自動化を可能にする。
Upset forgingEdit
アップセット鍛造は、その長さを圧縮することにより、ワークの直径を増加させます。 作り出される部分の数に基づいてこれは最も広く利用された鍛造材プロセスです。 動揺の鍛造材プロセスを使用して作り出される共通の部品の少数の例はエンジン弁、カップリング、ボルト、ねじおよび他の締める物である。
アップセット鍛造は、通常、クランクプレスと呼ばれる特別な高速機械で行われます。 機械は通常1つの場所からの次への工作物の速い交換を促進するために横の平面ではたらくようにセットアップされる動揺はまた縦の不安定な 最初の工作物は通常ワイヤーまたは棒ですが、ある機械は直径の棒25までcm(9.8inに)および1000トン上のの容量を受け入れることができます。 標準的な動揺させる機械は多数キャビティを含んでいる割れ目のダイスを用いる。 ダイスは工作物が1つのキャビティから次のキャビティに動くようにするには十分に開いた; その後、ダイが閉じ、見出しツール、またはラムがバーに対して縦方向に移動し、キャビティ内にそれを動揺させます。 キャビティすべてがあらゆる周期で利用されれば、終了する部品はこのプロセスを大量生産のために有利にさせるあらゆる周期と作り出されます。
鍛造動揺する部品を設計するときは、これらのルールに従う必要があります:
- 有害な座屈なしに一撃で動揺することができるサポートされてい
- 動揺の直径が株式の直径の1.5倍以下であれば、直径の三倍以上の株式の長さが正常に動揺することができます。
- 在庫の長さが在庫の直径の三倍以上を必要とする動揺では、キャビティの直径が在庫の直径の1.5倍以下である場合、ダイの面を超えてサポートされていない金属の長さはバーの直径を超えてはならない。
自動熱間鍛造edit
自動熱間鍛造プロセスは、室温で機械の一端にミル長さの鋼棒(通常は7m(23ft)の長さ)を供給し、熱間鍛造製品をもう一方の端 これはすべて急速に起こります;小さい部品は毎分180部(ppm)の率で作ることができ、より大きい90ppmの率で作ることができます。 部品は固体または空、円形または対称、6つまでのkg(13のlb)、および直径の18までcm(7.1inに)である場合もある。 このプロセスの主な利点は、その高い出力率と低コストの材料を受け入れる能力です。 少し労働は機械類を作動させるように要求されます。
フラッシュが生産されていないため、材料の節約は従来の鍛造よりも20-30%の間にあります。 最終製品は一貫した1,050°Cである(1,920°F)従って空冷はまだ容易に機械加工可能の部分で起因する(鍛造材の後で必要なアニーリングの欠乏である利点)。 許容は通常±0.3mm(0.012inに)、表面はきれいであり、草案角度は0.5から1°である。 接触時間が0.06秒のオーダーであるため、工具寿命は従来の鍛造のほぼ倍です。 欠点は、このプロセスはより小さな対称部品とコストでのみ実行可能であるということです。
このプロセスは、高出力誘導コイルを使用して60秒未満でバーを1,200〜1,300°C(2,190〜2,370°F)に加熱することから開始します。
バーを1,200〜1,300°C(2,190〜2,370°F)に加熱します。
それはローラーによってそれから除去され、ブランクにせん断され、そして動揺し、前もって形成され、最終的な造られ、そして穴をあける複数の連続した形 このプロセスはまた高速冷た形成操作と結合することができる。 一般に、冷間成形操作は、自動熱間鍛造の高速を維持しながら、冷間加工の利点を得ることができるように仕上げ段階を行う。このプロセスによって作られた部品の例は次のとおりです。
: LPのガスポンプのための車輪ハブの単位軸受け、伝達ギヤ、先を細くされた軸受の競争、ステンレス鋼のカップリングのフランジおよび首リング。 マニュアルトランスミッションギアは、冷間加工と組み合わせて使用される自動熱間鍛造の一例です。
ロール鍛造
ロール鍛造は、円形またはフラットバーストックの厚さが減少し、長さが増加するプロセスです。 ロール鍛造は、二つの円筒形または半円形のロールを使用して行われ、それぞれが一つ以上の形状の溝を含む。 熱くする棒はロールに挿入され、点に当るときロールは回り、機械を通って転がると同時に棒は漸進的に形づきます。 その後、ピースは次の溝のセットに移されるか、または回転して同じ溝に再挿入されます。 これは、所望の形状およびサイズが達成されるまで続く。 このプロセスの利点はフラッシュがないし、工作物に好ましい結晶粒構造を与えることである。
この方法を使用して製造された製品の例には、車軸、テーパレバー、板ばねが含まれます。
ネット形状とニアネット形状鍛造編集
このプロセスは、精密鍛造としても知られています。 後鍛造材操作と関連付けられる費用および無駄を最小にすることを開発した。 従って、精密鍛造材からの最終製品はほとんど最終的な機械化を必要としません。 原価節約はより少ない材料の使用から、およびこうして使用されるエネルギーのより少ないスクラップ、全面的な減少、および機械化の減少か除去得ら 精密鍛造材はまた草案、1°から0°のより少しを要求する。 このプロセスの欠点はコストであるため、大幅なコスト削減を達成できる場合にのみ実装されます。
冷間鍛造
ニアネット形状鍛造は、スラグ、バーまたはビレットを加熱せずに部品を鍛造する場合に最も一般的です。 アルミニウムは、最終的な形状に応じて冷間鍛造することができる一般的な材料である。 形成される部品の潤滑は、嵌合金型の寿命を延ばすために重要です。
誘導forgingEdit
上記のプロセスとは異なり、誘導鍛造は使用される加熱スタイルのタイプに基づいています。 上記のプロセスの多くは、この加熱方法と組み合わせて使用することができる。
多方向鍛造編集
多方向鍛造は、いくつかの方向に単一のステップでワークピースを形成しています。 多方向の形成は用具の建設的な手段によって起こる。 出版物のラムの縦の動きは横の方向の鍛造材出版物の力を配り、方向を変えるくさびを使用して方向を変えられる。
等温鍛造
等温鍛造は、材料とダイが同じ温度(iso-“等しい”を意味する)に加熱されるプロセスです。 断熱加熱は、材料の変形を支援するために使用され、ひずみ速度が高度に制御されることを意味する。 鋼よりも低い鍛造温度を有するアルミニウムを鍛造するために一般的に使用される。 アルミニウムのための鍛造材の温度は鋼鉄および極度の合金は930から1,260°cである場合もあるが、およそ430°C(806°F)です(1,710から2,300°F)。
:
- ニアネット形状が低い加工要件につながるため、より低いスクラップ率
- 部品の再現性
- より低い熱損失のために小さいマシンは、鍛造を行うために使用することができます
欠点:
- より高い温度と圧力を処理するための材料コストをダイ
- 均一な加熱システムが必要です
- 保護雰囲気や真空は、ダイと材料の酸化を低減するために
- 低生産率
Leave a Reply