Taonta

on olemassa monia erilaisia taontaprosesseja; ne voidaan kuitenkin ryhmitellä kolmeen pääluokkaan:
- vedetty: pituus kasvaa, poikkileikkaus pienenee
- järkyttää: pituus pienenee, poikkileikkaus kasvaa
- puristettu suljetussa puristusmuovissa: tuottaa monisuuntaisen virtauksen
yleisiä taontaprosesseja ovat: roll taonta, swaging, cogging, open-die taonta, impression-die taonta (lähellä die taonta), paina taonta, kylmä taonta automaattinen kuuma taonta ja järkyttävää.
TemperatureEdit
kaikki seuraavat taontaprosessit voidaan suorittaa eri lämpötiloissa; ne luokitellaan kuitenkin yleensä sen mukaan, onko metallin lämpötila yli vai alle uudelleenkiteyttämislämpötilan. Jos lämpötila on suurempi kuin materiaalin uudelleenkiteytys lämpötila katsotaan kuumataonta; jos lämpötila on alle materiaalin uudelleenkiteyttämislämpötilan, mutta yli 30% uudelleenkiteyttämislämpötilasta (absoluuttisella asteikolla), sitä pidetään lämpimänä taontana; jos se on alle 30% uudelleenkiteyttämislämpötilasta (yleensä huoneenlämpötila), sitä pidetään kylmänä taontana. Tärkein etu kuumataonta on, että se voidaan tehdä nopeammin ja täsmällisemmin, ja koska metalli on epämuodostunut työ kovettuminen vaikutukset kumotaan uudelleenkiteyttämällä prosessi. Kylmätaonta johtaa tyypillisesti kappaleen työstökarkaisuun.
Drop forgingEdit
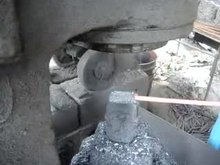
Play media
Pisarataonta on taontaprosessi, jossa vasara nostetaan ylös ja sitten ”pudotetaan” työkappaleeseen muotoutumaan muotin muodon mukaan. On olemassa kahdenlaisia pudota taonta: open-die pudota taonta ja impression-die (tai suljettu-die) pudota taonta. Kuten nimet viittaavat, ero on muotin, jossa edellinen ei täysin ympäröi työkappaleen, kun taas jälkimmäinen tekee.
Avohakkuupudotus


avotaonta tunnetaan myös Smith-taontana. Avomuottitaonnassa vasara iskee ja muokkaa työkappaletta, joka asetetaan paikallaan olevalle alasimelle. Avomuottitaonta on saanut nimensä siitä, että muotit (pinnat, jotka ovat kosketuksissa työkappaleen kanssa) eivät sulje työkappaletta, jolloin se virtaa, paitsi jos muotti koskettaa sitä. Käyttäjän on siis suunnattava ja sijoitettava työkappale halutun muodon saamiseksi. Stanssit ovat yleensä muodoltaan litteitä, mutta joissakin on erikoismuotoinen pinta erikoistoimintoja varten. Esimerkiksi muotin pinta voi olla pyöreä, kovera tai kupera, tai se voi olla reikien muodostamiseen tarkoitettu työkalu tai katkaistu työkalu.Avomuotti takeet voidaan työstää muotoja, jotka sisältävät levyjä, navat, lohkot, akselit (myös askel akselit tai laipat), hihat, sylinterit, flats, kuusiot, patruunat, levy, ja joitakin mukautettuja muotoja.Avomuotitaonta soveltuu lyhyisiin juoksuihin ja soveltuu taideseppiin ja tilaustöihin. Joissakin tapauksissa, avomuotti taonta voidaan käyttää karkea muoto harkot valmistaa niitä myöhempiä toimia. Avomuottitaonta voi myös suunnata viljaa lujuuden lisäämiseksi vaadittuun suuntaan.
Avomuotitaonnan edut
- pienempi tyhjien mahdollisuus
- parempi väsymisenkestävyys
- parempi mikrorakenne
- jatkuva raevirta
- hienompi raekoko
- suurempi lujuus
- parempi vaste lämpökäsittelylle
- sisäisen laadun paraneminen
- mekaanisten ominaisuuksien, sitkeyden ja iskunkestävyyden parempi luotettavuus
”cogging” on tangon peräkkäinen muodonmuutos sen pituudelta käyttäen avomuotista Drop Forgea. Sitä käytetään yleisesti työstää pala raaka-aineen oikea paksuus. Kun oikea paksuus on saavutettu oikea leveys saavutetaan ”reunus”.”Särmäys” on prosessi, jossa materiaali konsentroidaan koveran muotoisella avomuotilla. Prosessia kutsutaan ”särmäykseksi”, koska se suoritetaan yleensä työkappaleen päissä. ”Fullering” on samanlainen prosessi, joka ohentaa osia taonta käyttäen kupera muotoinen kuolee. Nämä prosessit valmistavat työkappaleet edelleen taonta prosesseja.
reunus
fullering
impression-Die forgingedit
impression-Die-taontaa kutsutaan myös ”umpitaonnaksi”. Impression-stanssissa metalli asetetaan muottia muistuttavaan muottiin, joka kiinnitetään alasimeen. Yleensä vasara kuolee on muotoiltu samoin. Vasara pudotetaan sitten työkappaleeseen, jolloin metalli virtaa ja täyttää muotin ontelot. Vasara on yleensä kosketuksissa työkappaleen kanssa millisekuntien asteikolla. Riippuen koosta ja monimutkaisuudesta osa, vasara voidaan pudottaa useita kertoja nopeasti peräkkäin. Ylimääräinen metalli puristetaan pois muotin onteloista muodostaen niin sanotun ”salaman”. Salama jäähtyy nopeammin kuin muu materiaali; Tämä viileä metalli on vahvempi kuin metalli kuolee, joten se auttaa estämään enemmän salaman muodostumista. Tämä myös pakottaa metallin täyttämään muotin ontelon kokonaan. Taonnan jälkeen salama poistetaan.
kaupallisessa impression-die-taonnassa työkappale siirretään yleensä sarjan onteloiden läpi muottiin, jotta se saadaan harkosta lopulliseen muotoon. Ensivaikutelmaa käytetään metallin jakamiseen karkeaan muotoon myöhempien onteloiden tarpeiden mukaisesti; tätä vaikutelmaa kutsutaan ”särmäykseksi”, ”fulleroinniksi” tai ”taivutusvaikutelmaksi”. Seuraavia onkaloita kutsutaan ”blokkaus” – onkaloiksi, joissa kappale työstyy muotoon, joka muistuttaa enemmän lopputuotetta. Nämä vaiheet yleensä antaa työkappaleen Antelias mutkia ja suuria fileet. Lopullinen muoto taotaan ” lopullinen ”tai” viimeistelijä ” vaikutelman ontelo. Jos on vain lyhyt juoksu osia tehdä, niin se voi olla taloudellisempaa kuolee puuttuu lopullinen vaikutelma onkalo ja sen sijaan kone lopulliset ominaisuudet.
Impression-die-taontaa on viime vuosina parannettu lisäämällä automaatiota, johon kuuluu induktiokuumennus, mekaaninen syöttö, sijoittelu ja manipulointi sekä osien suora lämpökäsittely taonnan jälkeen.Yksi muunnelma impression-die taonta kutsutaan ”flashless taonta”, tai”todellinen suljettu-die taonta”. Tämäntyyppisessä taonnassa muotin ontelot ovat täysin kiinni, mikä pitää työkappaleen muodostamasta salamaa. Suurin etu tässä prosessissa on, että vähemmän metallia menetetään flash. Välähdyksen osuus voi olla 20-45 prosenttia lähtöaineesta. Tämän prosessin haittoihin kuuluvat lisäkustannukset, jotka johtuvat monimutkaisemmasta muotin suunnittelusta ja paremman voitelun ja työkappaleen sijoittelun tarpeesta.
on olemassa muitakin osanmuodostuksen variaatioita, jotka yhdistävät impression-die-taontaa. Yksi menetelmä sisältää valu taonta esimuotin nestemäisestä metallista. Valu poistetaan, kun se on jähmettynyt, mutta kun se on vielä kuuma. Se on sitten valmis yhden ontelon kuolee. Salama leikataan, sitten osa sammutetaan kovetettu. Toinen muunnelma noudattaa samaa edellä kuvattua prosessia, paitsi esimuoto tuotetaan ruiskuttamalla laskeumaa metallipisaroiden muotoisiin kerääjiin (samanlainen kuin Osprey-prosessi).
suljetun muotin taonnalla on korkeat alkukustannukset johtuen muotin luomisesta ja työstömuotin onteloiden tekemiseen tarvittavasta suunnittelutyöstä. Sillä on kuitenkin alhaiset toistuvat kustannukset jokaiselle osalle, joten takeet tulevat taloudellisemmiksi suuremmalla tuotantomäärällä. Tämä on yksi tärkeimmistä syistä suljettu-die takeita käytetään usein auto-ja työkaluteollisuudessa. Toinen syy, miksi takeet ovat yleisiä näillä teollisuudenaloilla, on se, että takeiden lujuus / paino-suhde on yleensä noin 20 prosenttia suurempi kuin saman materiaalin valettujen tai työstettyjen osien.
impression-stanssitaonta ja työkalumuotit
Taontamuotit valmistetaan yleensä korkeaseoksesta tai työkaluteräksestä. Kuolee on iskunkestävä ja kulutusta kestävä, säilyttää lujuus korkeissa lämpötiloissa, on kyky kestää syklit nopea lämmitys ja jäähdytys. Paremman, taloudellisemman muotin tuottamiseksi pidetään yllä seuraavia standardeja:
- stanssiosaa pitkin yhtä, tasaista tasoa aina kun se on mahdollista. Jos ei, jakaus taso seuraa ääriviivat osan.
- jakauspinta on taonnan keskustan läpi kulkeva taso eikä lähellä ylä-tai alareunaa.
- riittävä syväys; yleensä vähintään 3° alumiinille ja 5° – 7° teräkselle.
- käytetään runsaasti fileitä ja säteitä.
- kylkiluut ovat matalat ja leveät.
- eri osat on tasapainotettu, jotta metallin virtauksessa ei olisi suuria eroja.
- kuituvirtauslinjoista otetaan täysi hyöty irti.
- mittatoleranssit eivät ole lähempänä kuin on tarpeen.
Barrelointi tapahtuu, kun työkappaleen ja suulakkeen tai punssin välisen kitkan vuoksi työkappale pullistuu keskeltä siten, että se muistuttaa tynnyriä. Tämä johtaa työkappaleen keskiosaan, joka joutuu kosketuksiin muotin sivujen kanssa nopeammin kuin jos kitkaa ei olisi, mikä lisää huomattavasti enemmän painetta, jota tarvitaan lyönnin viimeistelyyn taonta.
painallustaontamenetelmällä tuotetun teräsosan mittatoleranssit on esitetty alla olevassa taulukossa. Muotin sulkeminen vaikuttaa jakaustason kokoisiin mittoihin, ja ne ovat siksi riippuvaisia muotin kulumisesta ja lopullisen salaman paksuudesta. Mitat, jotka sisältyvät kokonaan yhteen muottisegmenttiin tai puolikkaaseen, voidaan säilyttää huomattavasti suuremmalla tarkkuudella.
Mass | Plus tolerance | |
---|---|---|
0.45 (1) | 0.15 (0, 006) | 0, 46 (0, 018) | 0, 91 (2) | 0, 20 (0, 008) | 0, 61 (0, 024) | 2, 27 (5) | 0, 25 (0, 010) | 0, 76 (0, 030) |
4, 54 (10) | 0.28 (0, 011) | 0, 84 (0, 033) | 9, 07 (20) | 0, 33 (0, 013) | 0, 99 (0, 039) |
22, 68 (50) | 1, 45 (0, 057) | 45, 36 (100) | 0, 74 (0, 029) | 2, 21 (0, 087) |
taonnassa käytetään voiteluainetta kitkan ja kulumisen vähentämiseksi. Sitä käytetään myös lämpöesteenä rajoittamaan lämmönsiirtoa työkappaleesta muottiin. Lopuksi voiteluaine toimii jakaus yhdiste estää osan tarttumisen kuolee.
paina takomalla
paina takomalla hitaasti jatkuvalla paineella tai voimalla, mikä eroaa pisaravasarataonnan lähes hetkellisestä iskusta. Aika, jonka muotit ovat kosketuksissa työkappaleen kanssa, mitataan sekunneissa (verrattuna drop-hammer-takojan millisekunteihin). Puristimen taonta voidaan tehdä joko kylmänä tai kuumana.
puristustaonnan tärkein etu pisarataontaan verrattuna on sen kyky muuttaa koko työkappaleen muotoaan. Drop-vasara taonta yleensä vain muuttaa työkappaleen pinnat kosketuksiin vasaran ja alasimen kanssa; työkappaleen sisäpuoli pysyy suhteellisen muotoutumattomana. Toinen prosessin etu on tieto uuden osan venymisnopeudesta. Säätämällä puristimen taontatoiminnon puristusnopeutta voidaan sisäistä rasitusta ohjata.
tähän prosessiin liittyy muutamia haittoja, joista suurin osa johtuu siitä, että työkappale on ollut kosketuksissa muotin kanssa näin pitkän ajan. Leikkaus on aikaa vievä prosessi johtuen askelten määrästä ja pituudesta. Työkappale jäähtyy nopeammin, koska muotit ovat kosketuksissa työkappaleen kanssa; muotit helpottavat huomattavasti enemmän lämmönsiirtoa kuin ympäröivä ilmakehä. Työkappaleen jäähtyessä siitä tulee vahvempi ja vähemmän sitkeä, mikä voi aiheuttaa halkeilua, jos muodonmuutos jatkuu. Siksi kuumennettuja muotteja käytetään yleensä vähentämään lämpöhäviötä, edistämään pintavirtausta ja mahdollistamaan hienompien yksityiskohtien ja tarkempien toleranssien tuottaminen. Työkappale voidaan myös joutua lämmittämään uudelleen.
korkeassa tuottavuudessa tehtynä puristustaonta on vasarataontaa taloudellisempaa. Toiminta luo myös tiiviimpiä toleransseja. Vasarataonnassa suuri osa työstä imeytyy koneisiin; puristustaonnassa työkappaleeseen käytetään suurempi osuus työstä. Toinen etu on, että toimintaa voidaan käyttää minkä tahansa kokoisen osan luomiseen, koska puristimen taontakoneen kokoa ei ole rajoitettu. Uudet puristustaontatekniikat ovat kyenneet luomaan korkeamman mekaanisen ja suuntauksen eheyden. Hapettumisen rajoittaminen osan uloimpiin kerroksiin johtaa valmiissa osassa tapahtuvaan mikrokytkentään.
Puristustaontaa voidaan käyttää kaikenlaisten taontatyyppien suorittamiseen, mukaan lukien avomuotti-ja impression-die-taonta. Impression-die press taonta vaatii yleensä vähemmän vetoa kuin pudota taonta ja on parempi mittatarkkuus. Myös paina takeet voidaan usein tehdä yksi sulkeminen kuolee, jolloin helppo automatisointi.
järkyttävä forgingEdit
järkyttynyt taonta lisää työkappaleen halkaisijaa puristamalla sen pituutta. Tuotettujen kappalemäärien perusteella tämä on yleisimmin käytetty taontaprosessi. Muutamia esimerkkejä tavanomaisista osista, jotka on valmistettu järkyttyneellä taontaprosessilla, ovat moottoriventtiilit, Kytkimet, pultit, ruuvit ja muut kiinnittimet.
järkyttynyt taonta tehdään yleensä erikoisissa nopeissa koneissa, joita kutsutaan kampipuristimiksi. Koneet on yleensä asetettu toimimaan vaakatasossa, jotta työkappaleiden nopea vaihto asemalta toiselle helpottuisi, mutta häirintä voidaan tehdä myös pystysuorassa kampipuristimessa tai hydraulipuristimessa. Alkuperäinen työkappale on yleensä lanka tai sauva, mutta jotkut koneet voivat hyväksyä baareja jopa 25 cm (9,8 in) halkaisijaltaan ja kapasiteetti on yli 1000 tonnia. Standardi järkyttävä kone työllistää split kuolee, jotka sisältävät useita onteloita. Suulakkeet ovat riittävän avoimet, jotta työkappale voi siirtyä yhdestä ontelosta seuraavaan; tämän jälkeen suulake sulkeutuu ja suuntatyökalu eli ram liikkuu pituussuunnassa tankoa vasten järkyttäen sen onteloon. Jos kaikki ontelot hyödynnetään joka kierroksella, valmis osa tuotetaan joka kierroksella, mikä tekee tästä prosessista edullisen massatuotannolle.
näitä sääntöjä on noudatettava suunniteltaessa osia taottaviksi:
- tukemattoman metallin pituus, joka voidaan järkyttää yhdellä iskulla ilman vahingollista vääntämistä, on rajoitettava kolme kertaa tangon halkaisijan suuruiseksi.
- kannan pituudet, jotka ovat yli kolme kertaa läpimitan suuruisia, voidaan järkyttää onnistuneesti edellyttäen, että järkytyksen halkaisija on enintään 1,5 kertaa kannan läpimitta.
- järkytyksessä, jossa kannan pituus on yli kolme kertaa kannan halkaisija ja jossa onkalon halkaisija on enintään 1,5 kertaa kannan halkaisija, ei tukemattoman metallin pituus suulakepinnan ulkopuolella saa ylittää tangon halkaisijaa.
Automaattinen kuumataonta
automaattisessa kuumataontaprosessissa syötetään tehtaan mittaisia terästankoja (tyypillisesti 7 metriä (23 jalkaa)) koneen toiseen päähän huoneenlämmössä ja toisesta päästä nousee kuumataottuja tuotteita. Tämä kaikki tapahtuu nopeasti; pieniä osia voidaan tehdä nopeudella 180 osaa minuutissa (ppm) ja suurempia voidaan tehdä nopeudella 90 ppm. Osat voivat olla kiinteitä tai onttoja, pyöreitä tai symmetrisiä, enintään 6 kg (13 lb) ja halkaisijaltaan jopa 18 cm (7,1 tuumaa). Tämän prosessin tärkeimmät edut ovat sen korkea tuotantonopeus ja kyky hyväksyä edullisia materiaaleja. Koneiden käyttö vaatii vain vähän työvoimaa.
ei ole valmistettu salamaa, joten materiaalisäästö on 20-30% tavanomaiseen taontaan verrattuna. Lopputuote on johdonmukainen 1,050 °C (1,920 °F), joten ilmajäähdytys johtaa osaan, joka on edelleen helposti työstettävissä (etuna on puute hehkutus tarvitaan taonta). Toleranssit ovat yleensä ±0,3 mm (0,012 in), pinnat ovat puhtaat ja vetokulmat 0,5-1°. Työkalun käyttöikä on lähes kaksinkertainen tavanomaiseen taontaan verrattuna, koska kosketusajat ovat 0,06 sekunnin luokkaa. Haittapuolena on, että tämä prosessi on mahdollista vain pienemmillä symmetrisillä osilla ja kustannuksilla; alkuinvestointi voi olla yli 10 miljoonaa dollaria, joten suuria määriä tarvitaan tämän prosessin perustelemiseksi.
prosessi aloitetaan kuumentamalla tanko 1 200-1 300 °C: seen (2 190-2 370 °F) Alle 60 sekunnissa suuritehoisia induktiokeloja käyttäen. Se on sitten descaled rullilla, leikataan aihioita, ja siirretään läpi useita peräkkäisiä muotoiluvaiheita, joiden aikana se on järkyttynyt, esimuotoiltu, lopullinen taottu, ja lävistetty (tarvittaessa). Tämä prosessi voidaan myös yhdistää nopeisiin kylmämuovaustoimintoihin. Yleensä kylmämuovausoperaatio tekee viimeistelyvaiheen niin, että kylmätyöskentelyn edut voidaan saada säilyttäen automaattisen kuumataonnan suuri nopeus.
esimerkkejä tällä prosessilla tehdyistä osista ovat: pyöränapayksikön Laakerit, vaihteistot, kartiorullalaakerikilpailut, ruostumattomasta teräksestä valmistetut kytkinlaipat ja LP-Kaasupullojen kaularenkaat. Manuaalivaihteiset vaihteistot ovat esimerkki automaattisesta kuumataonnasta, jota käytetään kylmätyön yhteydessä.
Valssitaonta
Valssitaonta on prosessi, jossa pyöreän tai litteän tankotaonnan paksuus pienenee ja pituus kasvaa. Rullataonta suoritetaan käyttämällä kahta lieriömäistä tai puolilieriömäistä rullaa, joista jokainen sisältää yhden tai useamman muotoisen uranäytteen. Rulliin työnnetään Lämmitetty tanko, ja kun se osuu johonkin kohtaan, rullat pyörivät ja tanko muotoutuu asteittain, kun se rullataan koneen läpi. Tämän jälkeen kappale siirretään seuraavaan urasarjaan tai käännetään ympäri ja asetetaan uudelleen samoihin uriin. Tämä jatkuu, kunnes haluttu muoto ja koko on saavutettu. Tämän prosessin etuna ei ole salamaa ja se antaa suotuisan viljarakenteen työkappaleeseen.
esimerkkejä tällä menetelmällä valmistetuista tuotteista ovat akselit, kapenevat vivut ja lehtijouset.
Net-muoto ja near-net-muoto takomalla
tätä prosessia kutsutaan myös tarkkuustaonnaksi. Se kehitettiin minimoimaan jälkitaontatoimiin liittyvät kustannukset ja jätteet. Siksi lopputuote tarkkuus taonta tarvitsee vain vähän tai ei lainkaan lopullinen koneistus. Kustannussäästöjä saadaan käyttämällä vähemmän materiaalia ja siten vähemmän romua, vähentämällä yleisesti käytettyä energiaa ja vähentämällä tai poistamalla työstö. Tarkkuustaonta vaatii myös vähemmän vetoa, 1° – 0°. Tämän prosessin haittapuolena ovat sen kustannukset, joten se toteutetaan vain, jos kustannusten merkittävä alentaminen voidaan saavuttaa.
Kylmätaonta
lähellä verkon muotoa taonta on yleisintä silloin, kun osat taotaan kuumentamatta etanaa, tankoa tai aihiota. Alumiini on yhteinen materiaali, joka voidaan kylmänä taottu riippuen lopullisesta muodosta. Muodostuvien osien voitelu on kriittistä pariutumisajan pidentämiseksi.
induktio forgingEdit
toisin kuin edellä mainitut prosessit, induktiotaonta perustuu käytettävään lämmitystyyliin. Monia edellä mainituista prosesseista voidaan käyttää yhdessä tämän lämmitysmenetelmän kanssa.
monisuuntainen taonta
monisuuntainen taonta on työkappaleen muodostamista yhdellä askeleella useampaan suuntaan. Monisuuntainen muotoilu tapahtuu työkalun rakentavilla toimenpiteillä. Puristinpuristimen pystysuuntainen liike ohjataan kiiloilla, jotka jakavat ja ohjaavat taontapuristimen voiman vaakasuoriin suuntiin.
isoterminen taonta
isoterminen taonta on prosessi, jossa materiaalit ja muotti kuumennetaan samaan lämpötilaan (iso – merkitys ”Yhtä suuri”). Adiabaattista kuumentamista käytetään materiaalin muodonmuutoksen apuna, eli venymisnopeudet ovat hyvin säädeltyjä. Käytetään yleisesti alumiinin taontaan, jonka taontalämpötila on alhaisempi kuin teräksillä. Alumiinin taontalämpötilat ovat noin 430 °C (806 °F), kun taas teräkset ja superseokset voivat olla 930-1 260 °C (1 710-2 300 °F).
etuudet:
- lähellä verkkomuotoja, jotka johtavat pienempiin työstövaatimuksiin ja siten alhaisempiin romunasteisiin
- osan uusittavuus
- pienemmän lämpöhäviön vuoksi pienempiä koneita voidaan käyttää taonnan tekemiseen
haitat:
- korkeampia muottimateriaalikustannuksia lämpötilojen ja paineiden käsittelyyn
- yhdenmukaisia lämmitysjärjestelmiä tarvitaan
- suojaavia ilmakehiä tai tyhjiötä muottien ja materiaalin hapettumisen vähentämiseksi
- alhaiset tuotantomäärät
Leave a Reply