Forgiatura

Ci sono molti diversi tipi di forgiatura disponibili; tuttavia, essi possono essere raggruppati in tre classi principali:
- Tirati fuori: aumenti di lunghezza, sezione diminuisce
- Sconvolto: diminuire della lunghezza, sezione trasversale aumenta
- Spremuto in chiusa di compressione muore: produce multidirezionale flusso
Comune forgiatura includono: rotolo forgiatura, foggiatura, cogging, open-die forgiatura, impression-die forgiatura (close die forgiatura), stampa forgiatura, stampaggio a freddo stampaggio a caldo automatico e sconvolgente.
TemperatureEdit
Tutti i seguenti processi di forgiatura possono essere eseguiti a varie temperature; tuttavia, sono generalmente classificati se la temperatura del metallo è superiore o inferiore alla temperatura di ricristallizzazione. Se la temperatura è superiore alla temperatura di ricristallizzazione del materiale è considerata forgiatura a caldo; se la temperatura è inferiore alla temperatura di ricristallizzazione del materiale ma superiore al 30% della temperatura di ricristallizzazione (su scala assoluta), viene considerata forgiatura a caldo; se inferiore al 30% della temperatura di ricristallizzazione (solitamente temperatura ambiente), viene considerata forgiatura a freddo. Il vantaggio principale di stampaggio a caldo è che può essere fatto in modo più rapido e preciso, e come il metallo è deformato lavoro indurimento effetti sono negati dal processo di ricristallizzazione. La forgiatura a freddo provoca tipicamente l’indurimento del pezzo.
Drop forgingEdit
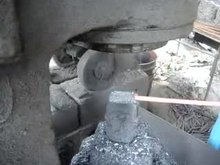
Play media
La forgiatura a goccia è un processo di forgiatura in cui un martello viene sollevato e quindi “lasciato cadere” sul pezzo in lavorazione per deformarlo in base alla forma dello stampo. Esistono due tipi di forgiatura a goccia: forgiatura a goccia aperta e forgiatura a goccia a stampo (o stampo chiuso). Come implicano i nomi, la differenza è nella forma dello stampo, con il primo che non racchiude completamente il pezzo, mentre il secondo lo fa.
Apri-cada die forgingEdit


Aprire-la forgiatura è anche conosciuto come smith, la forgiatura. Nella forgiatura a stampo aperto, un martello colpisce e deforma il pezzo, che viene posizionato su un’incudine fissa. La forgiatura a stampo aperto prende il nome dal fatto che gli stampi (le superfici a contatto con il pezzo) non racchiudono il pezzo, permettendogli di fluire tranne dove contattato dagli stampi. L’operatore deve quindi orientare e posizionare il pezzo per ottenere la forma desiderata. Gli stampi sono solitamente di forma piatta, ma alcuni hanno una superficie appositamente sagomata per operazioni specializzate. Ad esempio, uno stampo può avere una superficie rotonda, concava o convessa o essere uno strumento per formare fori o essere uno strumento di taglio.I forgiati open-die possono essere lavorati in forme che includono dischi, mozzi, blocchi, alberi (compresi alberi a gradini o con flange), manicotti, cilindri, appartamenti, esagoni, tondi, piastre e alcune forme personalizzate.La forgiatura a stampo aperto si presta a tirature brevi ed è adatta per la fucinatura artistica e il lavoro personalizzato. In alcuni casi, la forgiatura a stampo aperto può essere impiegata per lingotti di forma ruvida per prepararli per le operazioni successive. La forgiatura a stampo aperto può anche orientare il grano per aumentare la resistenza nella direzione richiesta.
i Vantaggi di forgiatura libera
- Ridotta possibilità di vuoti
- Migliore resistenza a fatica
- Migliorata la microstruttura
- Continuo flusso di grano
- granulometria più fine
- Maggiore resistenza
- Migliore risposta al trattamento termico
- Miglioramento della qualità interna
- Maggiore affidabilità delle proprietà meccaniche, la duttilità e la resistenza agli urti
“Cogging” è la successiva deformazione di un bar lungo la sua lunghezza, utilizzando un open-cada die forge. È comunemente usato per lavorare un pezzo di materia prima allo spessore adeguato. Una volta raggiunto lo spessore corretto, la larghezza corretta viene raggiunta tramite “bordatura”.”Bordatura” è il processo di concentrazione del materiale utilizzando un open-die a forma concava. Il processo è chiamato “bordatura” perché di solito viene eseguito sulle estremità del pezzo. “Fullering” è un processo simile che assottiglia le sezioni della forgiatura utilizzando uno stampo a forma convessa. Questi processi preparano i pezzi per ulteriori processi di forgiatura.
-
Bordatura
-
Fullering
Impressione-die forgingEdit
Impressione-la forgiatura è anche chiamato “stampaggio a caldo”. Nella forgiatura a stampo, il metallo viene posto in uno stampo simile a uno stampo, che è attaccato a un’incudine. Di solito, il dado martello è sagomato pure. Il martello viene quindi lasciato cadere sul pezzo, causando il flusso del metallo e riempiendo le cavità dello stampo. Il martello è generalmente in contatto con il pezzo in lavorazione sulla scala dei millisecondi. A seconda delle dimensioni e della complessità della parte, il martello può essere lasciato cadere più volte in rapida successione. Il metallo in eccesso viene spremuto dalle cavità dello stampo, formando ciò che viene definito “flash”. Il flash si raffredda più rapidamente rispetto al resto del materiale; questo metallo freddo è più forte del metallo nello stampo, quindi aiuta a prevenire la formazione di più flash. Ciò costringe anche il metallo a riempire completamente la cavità dello stampo. Dopo la forgiatura, il flash viene rimosso.
Nella forgiatura a stampo commerciale, il pezzo viene solitamente spostato attraverso una serie di cavità in uno stampo per passare da un lingotto alla forma finale. La prima impressione viene utilizzata per distribuire il metallo nella forma ruvida in base alle esigenze delle cavità successive; questa impressione è chiamata impressione “bordatura”, “fullering” o “piegatura”. Le seguenti cavità sono chiamate cavità “bloccanti”, in cui il pezzo sta lavorando in una forma che ricorda più da vicino il prodotto finale. Queste fasi di solito conferiscono al pezzo curve generose e filetti di grandi dimensioni. La forma finale è forgiata in una cavità di impressione” finale “o” finisher”. Se c’è solo una breve serie di parti da fare, allora può essere più economico per lo stampo manca una cavità impressione finale e invece macchina le caratteristiche finali.
Impression-die forgiatura è stata migliorata negli ultimi anni attraverso una maggiore automazione che comprende riscaldamento ad induzione, alimentazione meccanica, posizionamento e manipolazione, e il trattamento termico diretto delle parti dopo la forgiatura.Una variante della forgiatura a stampo è chiamata “forgiatura senza flash”o” vera forgiatura a stampo chiuso”. In questo tipo di forgiatura, le cavità dello stampo sono completamente chiuse, il che impedisce al pezzo di formare flash. Il principale vantaggio di questo processo è che meno metallo viene perso a lampeggiare. Flash può rappresentare dal 20 al 45% del materiale di partenza. Gli svantaggi di questo processo includono costi aggiuntivi dovuti a un design dello stampo più complesso e alla necessità di una migliore lubrificazione e posizionamento del pezzo.
Esistono altre varianti di formazione dei pezzi che integrano la forgiatura a stampo. Un metodo incorpora la fusione di una preforma di forgiatura da metallo liquido. Il getto viene rimosso dopo che si è solidificato, ma mentre è ancora caldo. Viene quindi finito in un unico stampo a cavità. Il flash viene tagliato,quindi la parte viene temprata. Un’altra variante segue lo stesso processo descritto sopra, tranne che la preforma è prodotta dalla deposizione a spruzzo di goccioline metalliche in collettori sagomati (simile al processo Osprey).
La forgiatura a stampo chiuso ha un costo iniziale elevato dovuto alla creazione di stampi e al lavoro di progettazione richiesto per realizzare cavità di stampo funzionanti. Tuttavia, ha bassi costi ricorrenti per ogni parte, quindi i pezzi fucinati diventano più economici con un maggiore volume di produzione. Questo è uno dei motivi principali per cui i forgiati a stampo chiuso vengono spesso utilizzati nelle industrie automobilistiche e degli utensili. Un altro motivo per cui i pezzi fucinati sono comuni in questi settori industriali è che i pezzi fucinati hanno generalmente un rapporto resistenza / peso superiore del 20% rispetto ai pezzi fusi o lavorati dello stesso materiale.
Progettazione di forgiati e utensili per impressionedit
Gli stampi per forgiatura sono solitamente realizzati in acciaio altolegato o per utensili. Le matrici devono essere resistenti agli urti e all’usura, mantenere la resistenza alle alte temperature, avere la capacità di resistere a cicli di riscaldamento e raffreddamento rapidi. Al fine di produrre uno stampo migliore e più economico vengono mantenuti i seguenti standard:
- Gli stampi si dividono su un singolo piano piano quando possibile. In caso contrario, il piano di separazione segue il contorno della parte.
- La superficie di separazione è un piano attraverso il centro della forgiatura e non vicino a un bordo superiore o inferiore.
- È previsto un tiraggio adeguato; di solito almeno 3° per l’alluminio e 5° a 7° per l’acciaio.
- Vengono utilizzati filetti e raggi generosi.
- Le costole sono basse e larghe.
- Le varie sezioni sono bilanciate per evitare un’estrema differenza nel flusso del metallo.
- Pieno vantaggio è preso di linee di flusso in fibra.
- Le tolleranze dimensionali non sono più vicine del necessario.
La barrellatura si verifica quando, a causa dell’attrito tra il pezzo da lavorare e lo stampo o la punzonatura, il pezzo da lavorare si rigonfia al centro in modo da assomigliare ad una canna. Ciò porta la parte centrale del pezzo a venire a contatto con i lati dello stampo prima che se non ci fosse attrito presente, creando un aumento molto maggiore della pressione necessaria per il punzone per finire la forgiatura.
Le tolleranze dimensionali di una parte in acciaio prodotta con il metodo di stampaggio a stampo sono descritte nella tabella seguente. Le dimensioni attraverso il piano di separazione sono influenzate dalla chiusura degli stampi e dipendono quindi dall’usura dello stampo e dallo spessore del flash finale. Le dimensioni che sono completamente contenute all’interno di un singolo segmento o metà dello stampo possono essere mantenute a un livello di precisione significativamente maggiore.
Massa | Meno tolleranza | Plus tolleranza |
---|---|---|
0.45 (1) | 0.15 (0.006) | 0.46 (0.018) |
0.91 (2) | 0.20 (0.008) | 0.61 (0.024) |
2.27 (5) | 0.25 (0.010) | 0.76 (0.030) |
4.54 (10) | 0.28 (0.011) | 0.84 (0.033) |
9.07 (20) | 0.33 (0.013) | 0.99 (0.039) |
22.68 (50) | 0.48 (0.019) | 1.45 (0.057) |
45.36 (100) | 0.74 (0.029) | 2.21 (0.087) |
Un lubrificante viene utilizzato quando la forgiatura per ridurre l’attrito e l’usura. Inoltre è usato come barriera termica per limitare il trasferimento di calore dal pezzo in lavorazione allo stampo. Infine, il lubrificante agisce come un composto di separazione per evitare che la parte si attacchi negli stampi.
Press forgingEdit
Press forging funziona applicando lentamente una pressione o una forza continua, che differisce dall’impatto quasi istantaneo della forgiatura a martello. La quantità di tempo in cui gli stampi sono a contatto con il pezzo viene misurata in secondi (rispetto ai millisecondi delle fucine a martello). L’operazione di stampaggio della pressa può essere eseguita a freddo oa caldo.
Il vantaggio principale della forgiatura della pressa, rispetto alla forgiatura a martello, è la sua capacità di deformare il pezzo completo. La forgiatura a martello di solito deforma solo le superfici del pezzo a contatto con il martello e l’incudine; l’interno del pezzo rimarrà relativamente indeformato. Un altro vantaggio del processo include la conoscenza della velocità di deformazione della nuova parte. Controllando il tasso di compressione dell’operazione di forgiatura della pressa, è possibile controllare la deformazione interna.
Questo processo presenta alcuni svantaggi, la maggior parte dei quali derivano dal fatto che il pezzo viene a contatto con gli stampi per un periodo di tempo così prolungato. L’operazione è un processo che richiede tempo a causa della quantità e della lunghezza dei passaggi. Il pezzo si raffredderà più velocemente perché gli stampi sono a contatto con il pezzo; gli stampi facilitano drasticamente più trasferimento di calore rispetto all’atmosfera circostante. Man mano che il pezzo si raffredda, diventa più forte e meno duttile, il che può indurre fessurazioni se la deformazione continua. Pertanto, gli stampi riscaldati vengono solitamente utilizzati per ridurre la perdita di calore, promuovere il flusso superficiale e consentire la produzione di dettagli più fini e tolleranze più strette. Potrebbe anche essere necessario riscaldare il pezzo.
Quando fatto in alta produttività, premere forgiatura è più economico di martello forgiatura. L’operazione crea anche tolleranze più strette. Nella forgiatura a martello gran parte del lavoro viene assorbito dal macchinario; quando nella forgiatura a pressa, la maggiore percentuale di lavoro viene utilizzata nel pezzo da lavorare. Un altro vantaggio è che l’operazione può essere utilizzata per creare qualsiasi parte di dimensioni perché non vi è alcun limite alle dimensioni della pressa. Le nuove tecniche di forgiatura della pressa sono state in grado di creare un più alto grado di integrità meccanica e di orientamento. Con il vincolo dell’ossidazione agli strati esterni della parte, si verificano livelli ridotti di microcracking nella parte finita.
Stampa forgiatura può essere utilizzato per eseguire tutti i tipi di forgiatura, tra cui open-die e impression-die forgiatura. Impression-die stampa forgiatura di solito richiede meno progetto di goccia forgiatura e ha una migliore precisione dimensionale. Inoltre, i pezzi fucinati della stampa possono essere fatti spesso in una chiusura degli stampi, tenendo conto automazione facile.
Sconvolto forgingEdit
La forgiatura sconvolta aumenta il diametro del pezzo comprimendo la sua lunghezza. In base al numero di pezzi prodotti, questo è il processo di forgiatura più utilizzato. Alcuni esempi di parti comuni prodotte utilizzando il processo di forgiatura sconvolto sono valvole del motore, giunti, bulloni, viti e altri elementi di fissaggio.
La forgiatura sconvolta viene solitamente eseguita in speciali macchine ad alta velocità chiamate presse a manovella. Le macchine sono solitamente impostate per lavorare sul piano orizzontale, per facilitare il rapido scambio di pezzi da una stazione all’altra, ma il ribaltamento può essere fatto anche in una manovella verticale o in una pressa idraulica. Il pezzo iniziale è solitamente filo o asta, ma alcune macchine possono accettare barre fino a 25 cm (9,8 in) di diametro e una capacità di oltre 1000 tonnellate. La macchina sconvolgente standard impiega matrici spaccate che contengono più cavità. Gli stampi si aprono abbastanza da consentire al pezzo di spostarsi da una cavità all’altra; gli stampi si chiudono e lo strumento di intestazione, o ram, si muove longitudinalmente contro la barra, sconvolgendola nella cavità. Se tutte le cavità sono utilizzate su ogni ciclo, quindi un pezzo finito sarà prodotto con ogni ciclo, che rende questo processo vantaggioso per la produzione di massa.
Queste regole devono essere seguite quando si progettano parti da sconvolgere forgiate:
- La lunghezza del metallo non supportato che può essere sconvolto in un colpo senza instabilità dannosa deve essere limitata a tre volte il diametro della barra.
- Lunghezze di magazzino maggiore di tre volte il diametro può essere sconvolto con successo, a condizione che il diametro del sconvolto non è più di 1.5 volte il diametro del magazzino.
- In un upset che richiede una lunghezza delle scorte superiore a tre volte il diametro delle scorte e dove il diametro della cavità non è superiore a 1,5 volte il diametro delle scorte, la lunghezza del metallo non supportato oltre la faccia dello stampo non deve superare il diametro della barra.
Forgiatura a caldo automaticamodifica
Il processo di forgiatura a caldo automatico prevede l’alimentazione di barre di acciaio di lunghezza del mulino (tipicamente 7 m (23 ft) di lunghezza) in un’estremità della macchina a temperatura ambiente e prodotti forgiati a caldo emergono dall’altra estremità. Tutto ciò avviene rapidamente; piccole parti possono essere fatte ad una velocità di 180 parti al minuto (ppm) e più grandi possono essere fatte ad una velocità di 90 ppm. Le parti possono essere solide o cave, rotonde o simmetriche, fino a 6 kg (13 lb) e fino a 18 cm (7,1 pollici) di diametro. I principali vantaggi di questo processo sono il suo alto tasso di produzione e la capacità di accettare materiali a basso costo. Poco lavoro è richiesto per azionare il macchinario.
Non viene prodotto alcun flash, quindi il risparmio di materiale è compreso tra il 20 e il 30% rispetto alla forgiatura convenzionale. Il prodotto finale è un costante 1.050 °C (1.920 °F) quindi il raffreddamento ad aria si tradurrà in una parte che è ancora facilmente lavorabile (il vantaggio è la mancanza di ricottura necessaria dopo la forgiatura). Le tolleranze sono di solito ±0,3 mm (0,012 pollici), le superfici sono pulite e gli angoli di sformo sono da 0,5 a 1°. La durata dell’utensile è quasi doppia rispetto alla forgiatura convenzionale perché i tempi di contatto sono dell’ordine di 0,06 secondi. Lo svantaggio è che questo processo è fattibile solo su parti simmetriche più piccole e costi; l’investimento iniziale può essere superiore a million 10 milioni, quindi sono necessarie grandi quantità per giustificare questo processo.
Il processo inizia riscaldando la barra da 1.200 a 1.300 °C (da 2.190 a 2.370 °F) in meno di 60 secondi utilizzando bobine di induzione ad alta potenza. Viene quindi disincrostato con rulli, tranciato in spazi vuoti e trasferito attraverso diverse fasi di formatura successive, durante le quali viene sconvolto, preformato, forgiato e forato (se necessario). Questo processo può anche essere accoppiato con operazioni di formatura a freddo ad alta velocità. Generalmente, l’operazione di formatura a freddo farà la fase di finitura in modo da ottenere i vantaggi della lavorazione a freddo, mantenendo l’alta velocità della forgiatura a caldo automatica.
Esempi di parti realizzate con questo processo sono: cuscinetti dell’unità del mozzo della ruota, ingranaggi di trasmissione, razze coniche del cuscinetto a rulli, flange dell’accoppiamento dell’acciaio inossidabile ed anelli del collo per le bombole di gas di LP. Gli ingranaggi del cambio manuale sono un esempio di stampaggio a caldo automatico utilizzato in combinazione con la lavorazione a freddo.
Forgiatura Rolledit
La forgiatura Roll è un processo in cui le barre tonde o piatte vengono ridotte di spessore e aumentate di lunghezza. La forgiatura del rotolo viene eseguita utilizzando due rulli cilindrici o semicilindrici, ciascuno contenente una o più scanalature sagomate. Una barra riscaldata viene inserita nei rulli e quando colpisce un punto i rulli ruotano e la barra viene progressivamente sagomata man mano che viene arrotolata attraverso la macchina. Il pezzo viene quindi trasferito alla successiva serie di scanalature o girato e reinserito nelle stesse scanalature. Questo continua fino a raggiungere la forma e le dimensioni desiderate. Il vantaggio di questo processo è che non c’è flash e conferisce una struttura di grano favorevole nel pezzo.
Esempi di prodotti realizzati con questo metodo includono assi, leve coniche e molle a balestra.
Net-shape e near-net-shape forgingEdit
Questo processo è noto anche come forgiatura di precisione. È stato sviluppato per ridurre al minimo i costi e gli sprechi associati alle operazioni di post-forgiatura. Pertanto, il prodotto finale da una forgiatura di precisione richiede poca o nessuna lavorazione finale. I risparmi sui costi sono ottenuti dall’uso di meno materiale e quindi meno rottami, dalla diminuzione complessiva dell’energia utilizzata e dalla riduzione o eliminazione della lavorazione. La forgiatura di precisione richiede anche meno di un tiraggio, da 1° a 0°. Lo svantaggio di questo processo è il suo costo, quindi viene implementato solo se è possibile ottenere una significativa riduzione dei costi.
Forgiatura a freddomodifica
La forgiatura vicino alla forma netta è più comune quando le parti vengono forgiate senza riscaldare la lumaca, la barra o la billetta. L’alluminio è un materiale comune che può essere forgiato a freddo a seconda della forma finale. La lubrificazione delle parti che si formano è fondamentale per aumentare la durata degli stampi di accoppiamento.
Forgiatura induzionemodifica
A differenza dei processi di cui sopra, la forgiatura ad induzione si basa sul tipo di stile di riscaldamento utilizzato. Molti dei processi di cui sopra possono essere utilizzati in combinazione con questo metodo di riscaldamento.
Forgiatura multidirezionalemodifica
La forgiatura multidirezionale sta formando un pezzo da lavorare in un unico passaggio in più direzioni. La formatura multidirezionale avviene attraverso misure costruttive dell’utensile. Il movimento verticale della pressa ram viene reindirizzato utilizzando cunei che distribuisce e reindirizza la forza della pressa forgiatura in direzioni orizzontali.
Forgiatura isotermicamodifica
La forgiatura isotermica è un processo mediante il quale i materiali e lo stampo vengono riscaldati alla stessa temperatura (iso – che significa “uguale”). Il riscaldamento adiabatico viene utilizzato per aiutare nella deformazione del materiale, il che significa che i tassi di deformazione sono altamente controllati. Comunemente usato per forgiare l’alluminio, che ha una temperatura di forgiatura inferiore rispetto agli acciai. Le temperature di forgiatura per l’alluminio sono di circa 430 ° C (806 ° F), mentre gli acciai e le superleghe possono essere da 930 a 1.260 °C (da 1.710 a 2.300 °F).
Vantaggi:
- Vicino al netto forme che portare a una riduzione dei requisiti di lavorazione e, quindi, la riduzione percentuale di scarto
- la Riproducibilità della parte
- a Causa della minore perdita di calore per le macchine di piccole dimensioni può essere utilizzato per la forgiatura
Svantaggi:
- Superiore morire i costi del materiale per gestire le temperature e le pressioni
- Uniforme sistemi di riscaldamento sono obbligatori
- Protezione in atmosfere di vuoto o di ridurre l’ossidazione degli stampi e materiale
- Bassi tassi di produzione
Leave a Reply