Kucie

dostępnych jest wiele różnych rodzajów procesów kucia, jednak można je pogrupować w trzy główne klasy:
- wyciągane: zwiększa się długość, zmniejsza się przekrój
- zdenerwowany: zmniejsza się długość, zwiększa się przekrój
- ściśnięty w zamkniętych matrycach kompresyjnych: wytwarza przepływ wielokierunkowy
typowe procesy kucia obejmują: kucie rolkowe, kucie, kucie, kucie na otwartej matrycy, kucie matrycowe (kucie matrycowe), kucie naciskowe, kucie na zimno automatyczne kucie na gorąco i denerwowanie.
Temperaturaedytuj
wszystkie poniższe procesy kucia mogą być wykonywane w różnych temperaturach; jednak są one zazwyczaj klasyfikowane według tego, czy temperatura metalu jest wyższa, czy niższa od temperatury rekrystalizacji. Jeśli temperatura jest wyższa niż temperatura rekrystalizacji materiału, uważa się, że kucie na gorąco; jeśli temperatura jest niższa od temperatury rekrystalizacji materiału, ale powyżej 30% temperatury rekrystalizacji (w skali bezwzględnej), uważa się, że jest to kucie ciepłe; jeśli poniżej 30% temperatury rekrystalizacji (Zwykle temperatura pokojowa), to uważa się, że jest to kucie na zimno. Główną zaletą kucia na gorąco jest to, że można to zrobić szybciej i precyzyjniej, a ponieważ metal jest zdeformowany, efekty utwardzania pracy są negowane przez proces rekrystalizacji. Kucie na zimno zazwyczaj skutkuje utwardzeniem pracy elementu.
drop forgingEdit
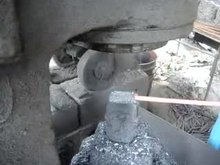
Odtwarzaj media
Kucie kroplowe to proces kucia, w którym młot jest podnoszony, a następnie „upuszczany” na obrabiany przedmiot, aby go odkształcić zgodnie z kształtem matrycy. Istnieją dwa rodzaje kucia kroplowego: kucie matrycowe i kucie matrycowe (lub kucie matrycowe). Jak sugerują nazwy, różnica polega na kształcie matrycy, przy czym pierwsza nie obejmuje w pełni przedmiotu obrabianego, podczas gdy druga robi.
Kucie metodą otwartej matrycy


kucie na otwartej matrycy jest również znane jako kucie kowalskie. W kuciu otwartym młotek uderza i odkształca obrabiany przedmiot, który jest umieszczony na nieruchomym kowadle. Kucie na otwartej matrycy bierze swoją nazwę od faktu, że matryce (powierzchnie, które mają kontakt z przedmiotem obrabianym) nie obejmują przedmiotu obrabianego, umożliwiając mu przepływ, z wyjątkiem przypadków, w których styka się z matrycami. Dlatego operator musi zorientować i ustawić obrabiany przedmiot, aby uzyskać pożądany kształt. Matryce są zwykle płaskie w kształcie, ale niektóre mają specjalnie ukształtowaną powierzchnię do specjalistycznych operacji. Na przykład matryca może mieć okrągłą, wklęsłą lub wypukłą powierzchnię lub być narzędziem do tworzenia otworów lub narzędziem odcięcia.Odkuwki z otwartą matrycą można obrabiać w kształty, które obejmują tarcze, piasty, bloki, wały (w tym wały stopniowe lub z kołnierzami), tuleje, cylindry, mieszkania, sześciokąty, okrągłe, płyty i niektóre niestandardowe kształty.Kucie na otwartej matrycy nadaje się do krótkich serii i nadaje się do kowalstwa artystycznego i pracy na zamówienie. W niektórych przypadkach kucie na otwartej matrycy może być stosowane do wlewków o szorstkim kształcie, aby przygotować je do kolejnych operacji. Kucie na otwartej matrycy może również zorientować ziarno, aby zwiększyć wytrzymałość w wymaganym kierunku.
zalety kucia na otwartej matrycy
- zmniejszona szansa na puste przestrzenie
- lepsza odporność na zmęczenie
- ulepszona mikrostruktura
- ciągły przepływ ziarna
- drobniejszy rozmiar ziarna
- większa wytrzymałość
- lepsza reakcja na obróbkę termiczną
- poprawa jakości wewnętrznej
- większa niezawodność właściwości mechanicznych, ciągliwości i odporności na uderzenia
„cogging” to następująca deformacja pręta wzdłuż jego długości za pomocą otwartej kuźni matrycowej. Jest powszechnie stosowany do obróbki kawałka surowca do odpowiedniej grubości. Po uzyskaniu odpowiedniej grubości uzyskuje się odpowiednią szerokość poprzez „obrzeża”.”Obrzeża” to proces zagęszczania materiału za pomocą wklęsłej matrycy otwartej. Proces ten nazywany jest „obrzeża”, ponieważ zwykle odbywa się na końcach obrabianego przedmiotu. „Fullering”to podobny proces, który rozrzedza sekcje kucia za pomocą wypukłej matrycy. Procesy te przygotowują detale do dalszych procesów kucia.
-
obrzeża
-
fullering
impression-Die forgingedit
impression-die forging jest również nazywany „kuciem matrycowym zamkniętym”. W kuciu matrycowym metal jest umieszczany w matrycy przypominającej formę, która jest przymocowana do kowadła. Zwykle matryca młotkowa jest również ukształtowana. Młotek jest następnie upuszczany na obrabiany przedmiot, powodując przepływ metalu i wypełnienie ubytków matrycy. Młotek jest na ogół w kontakcie z obrabianym przedmiotem w skali milisekund. W zależności od wielkości i złożoności części młotek może być wielokrotnie upuszczany w krótkim odstępie czasu. Nadmiar metalu jest wyciskany z zagłębień matrycy, tworząc to, co nazywa się „błyskiem”. Błysk chłodzi się szybciej niż reszta materiału; ten chłodny metal jest silniejszy niż metal w matrycy, więc pomaga zapobiegać powstawaniu większej ilości błysku. To również zmusza metal do całkowitego wypełnienia wnęki matrycy. Po kuciu lampa błyskowa jest usuwana.
w komercyjnym kuciu matrycowym, obrabiany przedmiot jest zwykle przesuwany przez szereg zagłębień w matrycy, aby dostać się z wlewka do ostatecznej postaci. Pierwsze wrażenie służy do rozprowadzania metalu w szorstki kształt zgodnie z potrzebami późniejszych ubytków; wrażenie to nazywa się „obrzeża”, „fullering” lub „bending” wrażenie. Następujące ubytki nazywane są ubytkami „blokującymi”, w których element pracuje w kształcie bardziej przypominającym produkt końcowy. Etapy te zwykle nadają przedmiotowi obfite zagięcia i duże filety. Ostateczny kształt wykuty jest w zagłębieniu wyciskowym” finalnym „lub” finiszerowym”. Jeśli jest tylko krótki cykl Części do zrobienia, to może być bardziej ekonomiczne dla matrycy do braku ostatecznego wycisku wnęki i zamiast maszyny końcowe cechy.
kucie matrycowe zostało ulepszone w ostatnich latach dzięki zwiększonej automatyzacji, która obejmuje nagrzewanie indukcyjne, podawanie mechaniczne, pozycjonowanie i manipulację oraz bezpośrednią obróbkę cieplną części po kuciu.Jedną z odmian kucia matrycowego jest nazywany „kucie bez błysku” lub „prawdziwe kucie matrycowe”. W tego typu kuciu wnęki matrycy są całkowicie zamknięte, co utrzymuje obrabiany przedmiot przed tworzeniem błysku. Główną zaletą tego procesu jest to, że mniej metalu jest tracony do lampy błyskowej. Flash może stanowić od 20 do 45% materiału wyjściowego. Wady tego procesu obejmują dodatkowe koszty ze względu na bardziej złożoną konstrukcję matrycy oraz potrzebę lepszego smarowania i umieszczenia przedmiotu obrabianego.
istnieją inne odmiany formowania części, które integrują kucie matrycowe. Jedna z metod obejmuje odlewanie preformy kucia z ciekłego metalu. Odlew jest usuwany po zestaleniu, ale wciąż gorący. Następnie kończy się w pojedynczej matrycy wnękowej. Lampa błyskowa jest przycinana, a następnie część hartowana. Inną odmianą jest ten sam proces, jak opisano powyżej, z wyjątkiem preform jest wytwarzany przez natryskiwanie osadzania kropelek metalu w kształcie kolektorów (podobny do procesu Osprey).
kucie matrycowe ma wysoki koszt początkowy ze względu na tworzenie matryc i wymagane prace projektowe w celu wykonania ubytków matrycy roboczej. Ma jednak niskie koszty powtarzalne dla każdej części, dzięki czemu odkuwki stają się bardziej ekonomiczne przy większej wielkości produkcji. Jest to jeden z głównych powodów, dla których odkuwki z matrycą zamkniętą są często stosowane w przemyśle motoryzacyjnym i narzędziowym. Innym powodem, dla którego odkuwki są powszechne w tych sektorach przemysłowych, jest to, że odkuwki mają zwykle o 20 procent wyższy stosunek wytrzymałości do masy w porównaniu z odlewanymi lub obrabianymi częściami z tego samego materiału.
projektowanie odkuwek matrycowych i oprzyrządowaniaedit
matryce do kucia są zwykle wykonane ze stali wysokostopowej lub narzędziowej. Matryce muszą być odporne na uderzenia i zużycie, utrzymywać wytrzymałość w wysokich temperaturach, mieć zdolność wytrzymywania cykli szybkiego ogrzewania i chłodzenia. Aby uzyskać lepszą, bardziej ekonomiczną matrycę, utrzymywane są następujące standardy:
- część matryc wzdłuż pojedynczej, płaskiej płaszczyzny, gdy tylko jest to możliwe. Jeśli nie, płaszczyzna podziału podąża za konturem części.
- powierzchnia podziału jest płaszczyzną przechodzącą przez środek kucia, a nie w pobliżu górnej lub dolnej krawędzi.
- zapewniony jest odpowiedni ciąg; zwykle co najmniej 3° dla aluminium i 5° do 7 ° dla stali.
- stosuje się obfite filety i promienie.
- żebra są niskie i szerokie.
- różne sekcje są zrównoważone, aby uniknąć ekstremalnych różnic w przepływie metalu.
- w pełni wykorzystuje się linie przepływu włókien.
- tolerancje wymiarowe nie są bliższe niż to konieczne.
Barrelling występuje, gdy z powodu tarcia między obrabianym przedmiotem a matrycą lub stemplem obrabiany przedmiot wybrzusza się w środku w taki sposób, aby przypominał lufę. Prowadzi to do tego, że centralna część obrabianego przedmiotu styka się z bokami matrycy szybciej niż gdyby nie było tarcia, tworząc znacznie większy wzrost ciśnienia wymaganego do stempla, aby zakończyć kucie.
tolerancje wymiarowe części stalowej wytwarzanej metodą kucia matrycowego są przedstawione w poniższej tabeli. Wymiary na płaszczyźnie podziału mają wpływ zamknięcia matryc, a zatem zależą od zużycia matrycy i grubości końcowego błysku. Wymiary, które są całkowicie zawarte w jednym segmencie matrycy lub połowie, mogą być utrzymywane na znacznie większym poziomie dokładności.
Masa | Minus tolerancja | Plus tolerancja |
---|---|---|
0,45 (1) | 0,15 (1) 0, 006) | 0, 46 (0, 018) |
0, 91 (2) | 0, 20 (0, 008) | 0, 61 (0, 024) |
2, 27 (5) | 0, 25 (0, 76 (0, 030) | |
4, 54 (10) | 0.28 (0, 011) | 0, 84 (0, 033) |
9, 07 (20) | 0, 33 (0, 013) | 0, 99 (0, 039) |
22, 68 (50) | 0, 48 (0, 019) | 1, 45 (0, 057) |
45, 36 (100) | 0, 74 (0, 029) | 2, 21 (0, 087) |
smar jest używany podczas kucia w celu zmniejszenia tarcia i zużycia. Jest również stosowany jako bariera termiczna, aby ograniczyć przenoszenie ciepła z przedmiotu obrabianego do matrycy. Wreszcie, smar działa jako związek rozdzielający, aby zapobiec przyklejaniu się części do matryc.
Kucie Prasoweedit
Kucie prasowe działa poprzez powolne stosowanie ciągłego nacisku lub siły, która różni się od niemal natychmiastowego uderzenia kucia młotkiem. Czas, przez jaki matryce stykają się z obrabianym przedmiotem, jest mierzony w sekundach (w porównaniu z milisekundami kuźni matrycowych). Operacja kucia prasy może być wykonywana na zimno lub na gorąco.
główną zaletą kucia prasowego, w porównaniu do kucia matrycowego, jest jego zdolność do odkształcania kompletnego przedmiotu obrabianego. Kucie z młotkiem typu drop-hammer Zwykle odkształca powierzchnie obrabianego przedmiotu w kontakcie z młotkiem i kowadłem; wnętrze obrabianego przedmiotu pozostanie stosunkowo nieodkształcone. Kolejną zaletą tego procesu jest znajomość stopnia odkształcenia nowej części. Kontrolując stopień sprężania operacji kucia prasy, można kontrolować odkształcenie wewnętrzne.
jest kilka wad tego procesu, większość wynika z tego, że przedmiot obrabiany jest w kontakcie z matrycami przez tak długi okres czasu. Operacja jest procesem czasochłonnym ze względu na ilość i długość kroków. Obrabiany przedmiot ostygnie szybciej, ponieważ matryce mają kontakt z obrabianym przedmiotem; matryce ułatwiają drastycznie większy transfer ciepła niż otaczająca atmosfera. Gdy przedmiot obrabiany chłodzi się, staje się silniejszy i mniej plastyczny, co może wywoływać pękanie, jeśli deformacja trwa. Dlatego ogrzewane matryce są zwykle stosowane w celu zmniejszenia strat ciepła, promowania przepływu powierzchniowego i umożliwienia produkcji drobniejszych szczegółów i bliższych tolerancji. Obrabiany przedmiot może również wymagać ponownego podgrzania.
Po wykonaniu z wysoką wydajnością kucie prasowe jest bardziej ekonomiczne niż kucie młotkowe. Operacja tworzy również bliższe tolerancje. W kuciu młotkowym dużo pracy jest pochłaniane przez maszynę; podczas kucia prasowego większy procent pracy jest wykorzystywany w obrabianym elemencie. Kolejną zaletą jest to, że operacja może być używana do tworzenia dowolnej wielkości części, ponieważ nie ma ograniczeń co do wielkości Maszyny do kucia prasowego. Nowe techniki kucia prasy były w stanie stworzyć wyższy stopień integralności mechanicznej i orientacji. Przez ograniczenie utleniania do zewnętrznych warstw części, zmniejszone poziomy mikropęknięć występują w gotowej części.
naciśnij kucie może być używany do wykonywania wszystkich rodzajów kucia, w tym open-die I wycisk matrycy kucia. Wyciskanie-die press kucie zwykle wymaga mniej zanurzenia niż kucie kroplowe i ma lepszą dokładność wymiarową. Ponadto odkuwki prasowe mogą być często wykonywane w jednym zamknięciu matryc, co pozwala na łatwą automatyzację.
Upset forgingEdit
Kucie wzburzone zwiększa średnicę obrabianego przedmiotu poprzez ściskanie jego długości. Na podstawie liczby wyprodukowanych sztuk jest to najczęściej stosowany proces kucia. Kilka przykładów części wspólnych produkowanych przy użyciu procesu kucia rozwartego to zawory silnika, złącza, śruby, wkręty i inne elementy złączne.
sfałszowane kucie odbywa się zwykle w specjalnych szybkich maszynach zwanych prasami korbowymi. Maszyny są zwykle ustawione do pracy w płaszczyźnie poziomej, aby ułatwić szybką wymianę detali z jednego stanowiska na drugie, ale można to również zrobić w pionowej prasie korbowej lub prasie hydraulicznej. Początkowy przedmiot obrabiany jest zwykle drutem lub prętem, ale niektóre maszyny mogą przyjmować pręty o średnicy do 25 cm (9,8 cala) i pojemności ponad 1000 ton. Standardowa maszyna do rozdrabniania wykorzystuje matryce dzielone, które zawierają wiele ubytków. Matryce są wystarczająco otwarte, aby umożliwić przemieszczanie się obrabianego przedmiotu z jednej wnęki do następnej; matryce następnie zamknąć i narzędzie pozycji, lub ram, a następnie przesuwa się wzdłużnie przeciwko bar, denerwując go do wnęki. Jeśli wszystkie wnęki są wykorzystywane w każdym cyklu, gotowa część zostanie wyprodukowana z każdym cyklem, co czyni ten proces korzystnym dla masowej produkcji.
zasady te muszą być przestrzegane przy projektowaniu części, które mają być sfałszowane:
- długość nieobsługiwanego metalu, który może być sfałszowany jednym uderzeniem bez szkodliwego wyboczenia, powinna być ograniczona do trzykrotności średnicy pręta.
- długości zapasów większe niż trzykrotność średnicy mogą być skutecznie zdenerwowane, pod warunkiem, że średnica zdenerwowania nie jest większa niż 1,5 razy średnica zapasu.
- w przypadku zdenerwowania wymagającego długości materiału większej niż trzykrotna średnica materiału, a gdzie średnica wnęki nie jest większa niż 1,5 razy średnica materiału, Długość nieobsługiwanego metalu poza powierzchnią matrycy nie może przekraczać średnicy pręta.
automatyczne kucie na gorąceedit
automatyczny proces kucia na gorąco polega na podawaniu prętów stalowych o długości młyna (zwykle 7 m (23 stopy)) na jednym końcu maszyny w temperaturze pokojowej, a gorące produkty kute wychodzą z drugiego końca. Wszystko to dzieje się szybko; małe części mogą być wykonane z szybkością 180 części na minutę (ppm)i większe mogą być wykonane z szybkością 90 ppm. Części mogą być solidne lub puste, okrągłe lub symetryczne, do 6 kg (13 funtów) i do 18 cm (7,1 cala) średnicy. Głównymi zaletami tego procesu są wysoka wydajność i zdolność do przyjmowania tanich materiałów. Do obsługi maszyn potrzeba niewiele pracy.
nie ma lampy błyskowej, więc oszczędność materiału wynosi od 20 do 30% w porównaniu z konwencjonalnym kuciem. Produkt końcowy ma stałą temperaturę 1050 °C (1920 °F), więc chłodzenie powietrzem spowoduje, że część będzie nadal łatwa do obróbki (zaletą jest brak wyżarzania wymaganego po kuciu). Tolerancje wynoszą zwykle ±0,3 mm (0,012 cala), powierzchnie są czyste, a kąty nachylenia wynoszą 0,5 do 1°. Trwałość narzędzia jest prawie dwukrotnie większa niż w przypadku kucia konwencjonalnego, ponieważ czasy kontaktu wynoszą 0,06 sekundy. Minusem jest to, że proces ten jest wykonalny tylko w przypadku mniejszych symetrycznych części i kosztów; początkowa inwestycja może wynosić ponad 10 milionów dolarów, więc wymagane są duże ilości, aby uzasadnić ten proces.
proces rozpoczyna się od podgrzania pręta do temperatury 1200-1300 °c (2190-2370 °F) w czasie krótszym niż 60 sekund przy użyciu cewek indukcyjnych dużej mocy. Następnie jest odkamieniany za pomocą rolek, ścinany na półfabrykaty i przenoszony przez kilka kolejnych etapów formowania, podczas których jest zdenerwowany, wstępnie uformowany, wykuty i przebity (jeśli to konieczne). Proces ten może być również połączony z szybkimi operacjami formowania na zimno. Ogólnie rzecz biorąc, operacja formowania na zimno wykona etap wykończeniowy, aby można było uzyskać zalety obróbki na zimno, przy zachowaniu wysokiej prędkości automatycznego kucia na gorąco.
przykładami części wykonanych w tym procesie są: łożyska piasty koła, przekładnie, łożyska stożkowe, kołnierze sprzęgające ze stali nierdzewnej i pierścienie szyjkowe do cylindrów gazowych LP. Przekładnie ręczne są przykładem automatycznego kucia na gorąco stosowanego w połączeniu z obróbką na zimno.
kucie Rolkoweedit
Kucie rolkowe to proces, w którym okrągły lub płaski pręt ma mniejszą grubość i większą długość. Kucie rolkowe odbywa się za pomocą dwóch walców cylindrycznych lub pół cylindrycznych, z których każda zawiera jeden lub więcej ukształtowanych rowków. Podgrzewany pręt jest wkładany do rolek, a gdy uderzy w miejsce, rolki obracają się, a pręt jest stopniowo kształtowany, gdy jest walcowany przez maszynę. Element jest następnie przenoszony do następnego zestawu rowków lub obracany i ponownie wkładany w te same rowki. Trwa to aż do uzyskania pożądanego kształtu i rozmiaru. Zaletą tego procesu jest brak błysku i nadaje korzystną strukturę ziarna do obrabianego przedmiotu.
przykładami produktów wytwarzanych tą metodą są osie, dźwignie stożkowe i resory piórowe.
kucie w kształcie siatki i w kształcie zbliżonej do sieciedytuj
ten proces jest również znany jako kucie precyzyjne. Został opracowany w celu zminimalizowania kosztów i odpadów związanych z operacjami po kuciu. Dlatego produkt końcowy z precyzyjnego kucia wymaga niewielkiej lub żadnej obróbki końcowej. Oszczędność kosztów uzyskuje się dzięki zastosowaniu mniejszej ilości materiału, a tym samym mniejszej ilości złomu, całkowitemu zmniejszeniu zużywanej energii oraz redukcji lub eliminacji obróbki skrawaniem. Kucie precyzyjne wymaga również mniej ciągu, 1° do 0°. Minusem tego procesu jest jego koszt, dlatego jest on realizowany tylko wtedy, gdy można osiągnąć znaczną redukcję kosztów.
kucie na Zimnoedit
w pobliżu kucia w kształcie siatki jest najczęściej spotykane, gdy części są kute bez podgrzewania ślimaka, pręta lub kęsa. Aluminium jest powszechnym materiałem, który może być kuty na zimno w zależności od ostatecznego kształtu. Smarowanie formowanych części ma kluczowe znaczenie dla zwiększenia żywotności matryc krytycznych.
kucie indukcyjne
w przeciwieństwie do powyższych procesów, kucie indukcyjne opiera się na rodzaju stosowanego stylu ogrzewania. Wiele z powyższych procesów można stosować w połączeniu z tą metodą ogrzewania.
kucie Wielokierunkoweedit
Kucie wielokierunkowe to formowanie przedmiotu obrabianego w jednym kroku w kilku kierunkach. Wielokierunkowe formowanie odbywa się poprzez konstruktywne środki narzędzia. Pionowy ruch tłoczni jest przekierowywany za pomocą klinów, które rozkładają i przekierowują siłę Prasy kucia w kierunku poziomym.
Kucie Izotermiczneedit
Kucie izotermiczne jest procesem, w którym materiały i matryca są podgrzewane do tej samej temperatury (iso – co oznacza „równe”). Ogrzewanie adiabatyczne służy do wspomagania deformacji materiału, co oznacza, że szybkość odkształceń jest wysoce kontrolowana. Powszechnie stosowany do kucia aluminium, które ma niższą temperaturę kucia niż stale. Temperatury kucia Aluminium wynoszą około 430 °c (806 °F), podczas gdy stale i Nadstopy mogą wynosić od 930 do 1260 °c (1710 do 2300 °f).
korzyści:
- w pobliżu kształtów siatki, które prowadzą do niższych wymagań dotyczących obróbki, a tym samym niższych ilości złomu
- odtwarzalność części
- ze względu na mniejsze straty ciepła mniejsze maszyny mogą być używane do kucia
wady:
- wyższe koszty materiału matrycy do obsługi temperatur i ciśnień
- wymagane są jednolite systemy grzewcze
- atmosfera ochronna lub próżnia w celu zmniejszenia utleniania matryc i materiału
- niskie tempo produkcji
Leave a Reply