Smide

det finns många olika typer av smidesprocesser tillgängliga; de kan dock grupperas i tre huvudklasser:
- dras ut: längd ökar, tvärsnitt minskar
- upprörd: längd minskar, tvärsnitt ökar
- pressas i slutna kompressions dör: producerar multidirectional flöde
vanliga smide processer inkluderar: rulla smide, swaging, cogging, open-die smide, intryck-die smide(nära dö smide), press smide, kall smide automatisk varm smide och upprörande.
TemperatureEdit
alla följande smidesprocesser kan utföras vid olika temperaturer; de klassificeras emellertid vanligtvis av om metalltemperaturen är över eller under omkristalliseringstemperaturen. Om temperaturen är över materialets omkristalliseringstemperatur anses den vara varmsmide; om temperaturen är under materialets omkristalliseringstemperatur men över 30% av omkristalliseringstemperaturen (i absolut skala) anses den varm smide; om under 30% av omkristalliseringstemperaturen (vanligtvis rumstemperatur) anses den kall smide. Den största fördelen med varmsmide är att det kan göras snabbare och exakt, och eftersom metallen deformeras arbete härdningseffekter negeras av omkristalliseringsprocessen. Kall smide resulterar vanligtvis i arbetshärdning av stycket.
Drop forgingEdit
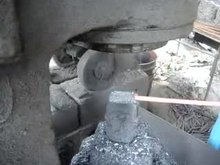
Play media
Drop smide är en smidesprocess där en hammare höjs och sedan ”tappas” på arbetsstycket för att deformera den enligt formen på munstycket. Det finns två typer av drop smide: open-die drop smide och impression-die (eller closed-die) drop smide. Som namnen antyder är skillnaden i form av munstycket, med den förstnämnda som inte helt omsluter arbetsstycket, medan den senare gör det.
open-die drop forgingEdit


Open-die smide är också känd som smide smide. I öppen form smide slår en hammare och deformerar arbetsstycket, som placeras på ett stationärt mothåll. Open-die smide får sitt namn från det faktum att formarna (ytorna som är i kontakt med arbetsstycket) inte omsluter arbetsstycket, så att det kan flöda utom när de kontaktas av formarna. Operatören behöver därför Orientera och placera arbetsstycket för att få önskad form. Formarna är vanligtvis plana, men vissa har en speciellt formad yta för specialoperationer. Till exempel kan en dö ha en rund, konkav eller konvex yta eller vara ett verktyg för att bilda hål eller vara ett avskärningsverktyg.Smide med öppen form kan bearbetas till former som inkluderar skivor, nav, block, axlar (inklusive stegaxlar eller med flänsar), ärmar, cylindrar, lägenheter, hexes, rundor, platta och några anpassade former.Open-die smide lämpar sig för korta körningar och är lämplig för konst smide och anpassade arbete. I vissa fall kan smide med öppen form användas för grovformade göt för att förbereda dem för efterföljande operationer. Smide med öppen form kan också orientera kornet för att öka styrkan i önskad riktning.
fördelar med Open-die smide
- minskad risk för tomrum
- bättre utmattningsbeständighet
- förbättrad mikrostruktur
- kontinuerligt kornflöde
- finare kornstorlek
- större styrka
- bättre svar på termisk behandling
- förbättring av intern kvalitet
- större tillförlitlighet av mekaniska egenskaper, duktilitet och slagmotstånd
”cogging” är den successiva deformationen av en stång längs dess längd med hjälp av en öppen formdroppsmedge. Det används ofta för att arbeta en bit råmaterial till rätt tjocklek. När rätt tjocklek uppnås uppnås rätt bredd via”kantning”.”Kantning” är processen att koncentrera material med en konkav formad öppen form. Processen kallas” kantning ” eftersom den vanligtvis utförs på arbetsstyckets ändar. ”Fullering” är en liknande process som tunnar ut delar av smide med hjälp av en konvex formad dö. Dessa processer förbereder arbetsstyckena för ytterligare smidesprocesser.
-
kant
-
fullering
impression-Die forgingedit
impression-die smide kallas också ”closed-die smide”. I impression-die smide placeras metallen i en form som liknar en form, som är fäst vid ett mothåll. Vanligtvis är hammarformen också formad. Hammaren tappas sedan på arbetsstycket, vilket får metallen att flöda och fylla formhålorna. Hammaren är i allmänhet i kontakt med arbetsstycket på skalan av millisekunder. Beroende på delens storlek och komplexitet kan hammaren tappas flera gånger i snabb följd. Överskott av metall pressas ut ur formhålorna och bildar det som kallas ”flash”. Blixten svalnar snabbare än resten av materialet; denna coola metall är starkare än metallen i munstycket, så det hjälper till att förhindra att mer blixt bildas. Detta tvingar också metallen att helt fylla formhålan. Efter smide avlägsnas blixten.
i kommersiell impression-die smide flyttas arbetsstycket vanligtvis genom en serie hålrum i en matris för att komma från en göt till den slutliga formen. Det första intrycket används för att fördela metallen i grov form i enlighet med behoven hos senare håligheter; detta intryck kallas ett ”kant”, ”fullering” eller ”böjning” intryck. Följande håligheter kallas” blockerande ” håligheter, där stycket arbetar i en form som mer liknar slutprodukten. Dessa steg ger vanligtvis arbetsstycket generösa böjningar och stora fileter. Den slutliga formen är smidd i en” slutlig ”eller” efterbehandlare ” intryckshålighet. Om det bara finns en kort körning av delar som ska göras, kan det vara mer ekonomiskt för munstycket att sakna ett slutligt intryckshålighet och istället bearbeta de slutliga funktionerna.
Impression-die smide har förbättrats under de senaste åren genom ökad automatisering som inkluderar induktionsuppvärmning, mekanisk matning, positionering och manipulation och direkt värmebehandling av delar efter smide.En variation av intryck-die smide kallas ”flashless smide”, eller ”true closed-die smide”. I denna typ av smide är formhålorna helt stängda, vilket håller arbetsstycket från att bilda blixt. Den stora fördelen med denna process är att mindre metall går förlorad för blixt. Flash kan stå för 20 till 45% av utgångsmaterialet. Nackdelarna med denna process inkluderar extra kostnad på grund av en mer komplex formkonstruktion och behovet av bättre smörjning och arbetsstycksplacering.
det finns andra variationer av delbildning som integrerar intryck-die smide. En metod innefattar gjutning av en smidespreform från flytande metall. Gjutningen avlägsnas efter att den har stelnat, men medan den fortfarande är varm. Den avslutas sedan i en enda hålrum dö. Blixten är trimmad, sedan släcks delen härdad. En annan variation följer samma process som beskrivits ovan, förutom att förformen framställs genom sprutavsättning av metalldroppar i formade samlare (liknande Fiskgjuseprocessen).
Closed-die smide har en hög initial kostnad på grund av skapandet av dör och krävs designarbete för att göra arbets dö hålrum. Det har dock låga återkommande kostnader för varje del, vilket smide blir mer ekonomiskt med större produktionsvolym. Detta är en av de främsta anledningarna till att smidesmide ofta används inom fordons-och verktygsindustrin. En annan anledning smide är vanligt i dessa industrisektorer är att smide i allmänhet har ungefär en 20 procent högre styrka-till-vikt-förhållande jämfört med gjutna eller bearbetade delar av samma material.
design av impression-die smide och toolingEdit
smide dör är vanligtvis gjorda av höglegerat eller verktygsstål. Dies måste vara slag-och slitstarka, bibehålla styrkan vid höga temperaturer, ha förmåga att motstå cykler med snabb uppvärmning och kylning. För att producera en bättre, mer ekonomisk dö upprätthålls följande standarder:
- dördelen längs ett enda, platt plan när det är möjligt. Om inte, följer avskiljningsplanet delens kontur.
- avskiljningsytan är ett plan genom smidets centrum och inte nära en övre eller nedre kant.
- lämpligt utkast tillhandahålls; vanligtvis minst 3 kg för aluminium och 5-7 kg för stål.
- generösa fileter och radier används.
- revbenen är låga och breda.
- de olika sektionerna är balanserade för att undvika extrem skillnad i metallflöde.
- Full fördel tas av fiberflödeslinjer.
- Dimensionstoleranser är inte närmare än nödvändigt.
Barrelling uppstår när arbetsstycket, på grund av friktion mellan arbetsstycket och munstycket eller stansen, buktar i mitten på ett sådant sätt att det liknar ett fat. Detta leder till att den centrala delen av arbetsstycket kommer i kontakt med sidorna på munstycket tidigare än om det inte fanns någon friktion närvarande, vilket skapar en mycket större ökning av trycket som krävs för stansen för att avsluta smiden.
dimensionstoleranserna för en ståldel framställd med hjälp av avtryckssmidesmetoden beskrivs i tabellen nedan. Dimensionerna över avskiljningsplanet påverkas av stängningen av formarna och är därför beroende av dysslitage och tjockleken på den slutliga blixten. Dimensioner som är helt inneslutna i ett enda formsegment eller halv kan bibehållas på en betydligt högre nivå av noggrannhet.
massa | Minus tolerans | Plus tolerans |
---|---|---|
0,45 (1) | 0,15 (0, 006) | 0, 46 (0, 018) |
0, 91 (2) | 0, 20 (0, 008) | 0, 61 (0, 024) |
2, 27 (5) | 0, 25 (0, 010) | 0, 76 (0, 030) |
4, 54 (10) | 0.28 (0, 011) | 0, 84 (0, 033) |
9, 07 (20) | 0, 33 (0, 013) | 0, 99 (0, 039) |
22, 68 (50) | 0,48 (0,019) | 1,45 (0,057) |
45,36 (100) | 0,74 (0,029) | 2,21 (0,087) |
ett smörjmedel används vid smidning för att minska friktion och slitage. Det används också som en termisk barriär för att begränsa värmeöverföringen från arbetsstycket till munstycket. Slutligen fungerar smörjmedlet som en avskiljningsförening för att förhindra att delen fastnar i formarna.
Press forgingEdit
Press smide fungerar genom att långsamt applicera ett kontinuerligt tryck eller kraft, vilket skiljer sig från den nästan ögonblickliga effekten av drop-hammer smide. Den tid som formarna är i kontakt med arbetsstycket mäts i sekunder (jämfört med millisekunder av drop-hammer smides). Press smide operation kan göras antingen kallt eller varmt.
den största fördelen med press smide, jämfört med drop-hammer smide, är dess förmåga att deformera hela arbetsstycket. Drop-hammer smide deformerar vanligtvis bara ytorna på arbetsstycket i kontakt med hammaren och städet; arbetsstyckets inre förblir relativt odeformerat. En annan fördel med processen inkluderar kunskapen om den nya delens belastningsgrad. Genom att styra kompressionshastigheten för presssmideoperationen kan den inre stammen styras.
det finns några nackdelar med denna process, mest härrör från arbetsstycket är i kontakt med formarna under en sådan längre tid. Operationen är en tidskrävande process på grund av mängden och längden på stegen. Arbetsstycket kommer att svalna snabbare eftersom formarna är i kontakt med arbetsstycket; formarna underlättar drastiskt mer värmeöverföring än den omgivande atmosfären. När arbetsstycket svalnar blir det starkare och mindre duktilt, vilket kan inducera sprickbildning om deformationen fortsätter. Därför används uppvärmda dör vanligtvis för att minska värmeförlusten, främja ytflöde och möjliggöra produktion av finare detaljer och närmare toleranser. Arbetsstycket kan också behöva värmas upp igen.
När det görs i hög produktivitet är press smide mer ekonomiskt än hammarsmide. Operationen skapar också närmare toleranser. I hammarsmide absorberas mycket av arbetet av maskinerna; vid presssmide används den större andelen arbete i arbetsstycket. En annan fördel är att operationen kan användas för att skapa någon storlek del eftersom det inte finns någon gräns för storleken på press smide maskin. Nya press smide tekniker har kunnat skapa en högre grad av mekanisk och orientering integritet. Genom begränsning av oxidation till de yttre skikten av delen uppträder reducerade nivåer av mikrokrackning i den färdiga delen.
Press smide kan användas för att utföra alla typer av smide, inklusive open-die och impression-die smide. Impression-die press smide kräver vanligtvis mindre drag än drop smide och har bättre dimensionell noggrannhet. Dessutom kan press smide ofta göras i en stängning av formarna, vilket möjliggör enkel automatisering.
upprörd forgingEdit
upprörd smide ökar arbetsstyckets diameter genom att komprimera dess längd. Baserat på antalet producerade bitar är detta den mest använda smidesprocessen. Några exempel på vanliga delar som produceras med hjälp av den upprörda smidesprocessen är motorventiler, kopplingar, bultar, skruvar och andra fästelement.
upprörd smide görs vanligtvis i speciella höghastighetsmaskiner som kallas vevpressar. Maskinerna är vanligtvis inställda för att fungera i horisontalplanet för att underlätta snabb utbyte av arbetsstycken från en station till en annan, men upprörande kan också göras i en vertikal vevpress eller en hydraulisk press. Det ursprungliga arbetsstycket är vanligtvis tråd eller stång, men vissa maskiner kan acceptera stänger upp till 25 cm (9,8 tum) i diameter och en kapacitet på över 1000 ton. Den vanliga upprörande maskinen använder delade dör som innehåller flera håligheter. Formarna är tillräckligt öppna för att arbetsstycket ska kunna röra sig från ett hålrum till nästa; formarna stängs sedan och rubrikverktyget, eller ram, rör sig sedan i längdriktningen mot stången och stör den in i hålrummet. Om alla hålrummen används på varje cykel, kommer en färdig del att produceras med varje cykel, vilket gör denna process fördelaktig för massproduktion.
dessa regler måste följas vid utformning av delar som ska vara upprörda smidda:
- längden på metall som inte stöds som kan vara upprörd i ett slag utan skadlig knäckning bör begränsas till tre gånger stångens diameter.
- längder av lager större än tre gånger diametern kan vara upprörd framgångsrikt, förutsatt att diametern på upprörd inte är mer än 1,5 gånger stamens diameter.
- i en upprördhet som kräver lagerlängd som är större än tre gånger stamens diameter, och där hålrummets diameter inte är mer än 1,5 gånger stamens diameter, får längden på metall som inte stöds bortom matrisens yta inte överstiga stångens diameter.
Automatic hot forgingEdit
den automatiska varmsmidesprocessen innebär matning av stålstänger i kvarnlängd (vanligtvis 7 m (23 fot) långa) i ena änden av maskinen vid rumstemperatur och heta smidda produkter kommer ut från den andra änden. Allt detta sker snabbt; små delar kan tillverkas med en hastighet av 180 delar per minut (ppm) och större kan göras med en hastighet av 90 ppm. Delarna kan vara fasta eller ihåliga, runda eller symmetriska, upp till 6 kg (13 lb) och upp till 18 cm (7,1 tum) i diameter. De främsta fördelarna med denna process är dess höga produktionshastighet och förmåga att acceptera billiga material. Lite arbete krävs för att använda maskinen.
det finns ingen blixt produceras så materialbesparingar är mellan 20 och 30% jämfört med konventionell smide. Den slutliga produkten är en konsekvent med 1 050 °C (1,920 °F) så luftkylning kommer att resultera i en del som är fortfarande lätt bearbetbara (fördelen är brist på glödgning krävs efter smide). Toleranser är vanligtvis 0,3 mm (0,012 tum), ytorna är rena och dragvinklarna är 0,5 till 1 kg. Verktygslivslängden är nästan dubbelt så stor som konventionell smide eftersom kontakttiderna är i storleksordningen 0,06 sekunder. Nackdelen är att denna process endast är möjlig på mindre symmetriska delar och kostnader; den initiala investeringen kan vara över 10 miljoner dollar, så stora mängder krävs för att motivera denna process.
processen börjar med att värma stången till 1 200 till 1 300 cc (2 190 till 2 370 CCF) på mindre än 60 sekunder med hjälp av induktionsspolar med hög effekt. Den avkalkas sedan med rullar, skärs i ämnen och överförs genom flera på varandra följande formningssteg, under vilka den är upprörd, förformad, slutlig Smidd och genomborrad (om nödvändigt). Denna process kan också kombineras med höghastighets kallformningsoperationer. Generellt kommer kallformningsoperationen att göra slutskedet så att fördelarna med kallbearbetning kan erhållas, samtidigt som den höga hastigheten för automatisk varmsmide bibehålls.
exempel på delar gjorda av denna process är: hjulnavenhetslager, växellådor, avsmalnande rullager, kopplingsflänsar i rostfritt stål och nackringar för LP-gasflaskor. Manuella växellådor är ett exempel på automatisk varmsmide som används i samband med kallbearbetning.
Roll forgingEdit
Roll smide är en process där rund eller platt bar lager reduceras i tjocklek och ökad längd. Rullsmide utförs med användning av två cylindriska eller halvcylindriska rullar, var och en innehållande en eller flera formade spår. En uppvärmd stång sätts in i rullarna och när den träffar en plats roterar rullarna och stången formas gradvis när den rullas genom maskinen. Stycket överförs sedan till nästa uppsättning spår eller vänds om och sätts tillbaka i samma spår. Detta fortsätter tills önskad form och storlek uppnås. Fördelen med denna process är att det inte finns någon blixt och det ger en gynnsam kornstruktur i arbetsstycket.
exempel på produkter som produceras med denna metod inkluderar axlar, avsmalnande spakar och bladfjädrar.
net-shape och near-net-shape forgingEdit
denna process är också känd som precision smide. Det utvecklades för att minimera kostnader och avfall i samband med efter smide. Därför behöver slutprodukten från en precisionssmide liten eller ingen slutlig bearbetning. Kostnadsbesparingar uppnås genom användning av mindre material och därmed mindre skrot, den totala minskningen av energi som används och minskning eller eliminering av bearbetning. Precisionssmide kräver också mindre av ett utkast, 1 kg till 0 kg. Nackdelen med denna process är dess kostnad, därför implementeras den endast om betydande kostnadsminskning kan uppnås.
kall forgingEdit
nära nätform smide är vanligast när delar är smidda utan uppvärmning av slug, bar eller billet. Aluminium är ett vanligt material som kan vara kallt smidd beroende på slutlig form. Smörjning av de delar som bildas är avgörande för att öka parningens livslängd.
induktion forgingEdit
Till skillnad från ovanstående processer är induktionsmide baserad på vilken typ av uppvärmningsstil som används. Många av ovanstående processer kan användas i samband med denna uppvärmningsmetod.
multidirectional forgingEdit
Multidirectional smide bildar ett arbetsstycke i ett enda steg i flera riktningar. Den multidirektionella formningen sker genom konstruktiva åtgärder av verktyget. Den vertikala rörelsen av pressramen omdirigeras med kilar som distribuerar och omdirigerar kraften hos smidespressen i horisontella riktningar.
isotermisk forgingEdit
isotermisk smide är en process genom vilken materialen och munstycket upphettas till samma temperatur (iso – vilket betyder ”lika”). Adiabatisk uppvärmning används för att hjälpa till vid deformation av materialet, vilket innebär att belastningshastigheterna är mycket kontrollerade. Vanligen används för smide aluminium, som har en lägre smide temperatur än stål. Smidningstemperaturer för aluminium är cirka 430 kg c (806 kg F), medan stål och superlegeringar kan vara 930 till 1 260 kg C (1 710 till 2 300 kg f).
fördelar:
- nära nätformer som leder till lägre bearbetningskrav och därmed lägre skrothastigheter
- reproducerbarhet av delen
- på grund av den lägre värmeförlusten kan mindre maskiner användas för att göra smidningen
nackdelar:
- högre materialkostnader för att hantera temperaturer och tryck
- enhetliga värmesystem krävs
- skyddande atmosfärer eller vakuum för att minska oxidationen av matriserna och materialet
- låga produktionshastigheter
Leave a Reply