Smedning

Der er mange forskellige former for smedningsprocesser tilgængelige; de kan dog grupperes i tre hovedklasser:
- trukket ud: længde øges, tværsnit falder
- forstyrret: længde falder, tværsnit øges
- klemt i lukkede kompressionsdyser: producerer multidirektionel strømning
almindelige smedningsprocesser inkluderer: roll smedning, svingning, cogging, åben-dør smedning, indtryk-dør smedning(tæt dør smedning), tryk smedning, kold smedning automatisk varm smedning og forstyrrende.
Temperaturredit
alle følgende smedningsprocesser kan udføres ved forskellige temperaturer; de klassificeres dog generelt efter, om metaltemperaturen er over eller under omkrystalliseringstemperaturen. Hvis temperaturen er over materialets omkrystallisationstemperatur, betragtes det som varm smedning; hvis temperaturen er under materialets omkrystalliseringstemperatur, men over 30% af omkrystalliseringstemperaturen (i absolut skala) betragtes det som varm smedning; hvis Under 30% af omkrystalliseringstemperaturen (normalt stuetemperatur) betragtes det som kold smedning. Den største fordel ved varm smedning er, at det kan gøres hurtigere og mere præcist, og som metallet er deformeret arbejde hærdning effekter negeres af omkrystallisationsprocessen. Kold smedning resulterer typisk i arbejdshærdning af stykket.
Drop forgingEdit
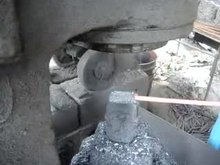
Play media
Drop smedning er en smedning proces, hvor en hammer hæves og derefter “faldt” på emnet for at deformere det i henhold til formen af matricen. Der er to Typer drop smedning: open-die drop smedning og indtryk-die (eller lukket-die) drop smedning. Som navnene antyder, er forskellen i form af matricen, hvor førstnævnte ikke helt omslutter emnet, mens sidstnævnte gør det.
open-die drop smedningedit

åben smedning er også kendt som smedning. Ved åben smedning rammer en hammer og deformerer emnet, som er anbragt på en stationær ambolt. Open-die smedning får sit navn fra det faktum, at matricerne (overfladerne, der er i kontakt med emnet) ikke omslutter emnet, så det kan strømme, undtagen hvor det kontaktes af matricerne. Operatøren skal derfor Orientere og placere emnet for at få den ønskede form. Matricerne er normalt flade i form, men nogle har en specielt formet overflade til specialiserede operationer. For eksempel kan en matrice have en rund, konkav eller konveks overflade eller være et værktøj til at danne huller eller være et afskæringsværktøj.Smedegods med åben form kan bearbejdes i former, der inkluderer skiver, nav, blokke, aksler (inklusive trinaksler eller med flanger), ærmer, cylindre, lejligheder, sekskanter, runder, plade og nogle brugerdefinerede former.Open-die smedning egner sig til korte kørsler og er passende for kunst smedning og brugerdefinerede arbejde. I nogle tilfælde kan smedning med åben form anvendes til barrer i ru form for at forberede dem til efterfølgende operationer. Open-die smedning kan også orientere kornet for at øge styrken i den ønskede retning.
fordele ved åben smedning
- Reduceret chance for hulrum
- bedre træthedsmodstand
- forbedret mikrostruktur
- kontinuerlig kornstrøm
- finere kornstørrelse
- større styrke
- bedre respons på termisk behandling
- forbedring af intern kvalitet
- større pålidelighed af mekaniske egenskaber, duktilitet og slagfasthed
“cogging” er den successive deformation af en stang langs dens længde ved hjælp af en open-die drop smedje. Det er almindeligt anvendt til at arbejde et stykke råmateriale til den rette tykkelse. Når den korrekte tykkelse er opnået, opnås den korrekte bredde via”kantning”.”Kantning” er processen med at koncentrere materiale ved hjælp af en konkavformet åben dør. Processen kaldes” kantning”, fordi den normalt udføres på enderne af emnet. “Fullering” er en lignende proces, der tynder dele af smedningen ud ved hjælp af en konveks formet matrice. Disse processer forbereder emnerne til yderligere smedningsprocesser.
-
kantning
fullering
impression-die smedningedit
impression-die smedning kaldes også “closed-die smedning”. I impression-die smedning placeres metallet i en matrice, der ligner en form, der er fastgjort til en ambolt. Normalt er hammeren også formet. Hammeren falder derefter på emnet, hvilket får metallet til at strømme og fylde hulrummene. Hammeren er generelt i kontakt med emnet på skalaen af millisekunder. Afhængig af delens størrelse og kompleksitet kan hammeren tabes flere gange i hurtig rækkefølge. Overskydende metal presses ud af hulrummene og danner det, der kaldes “flash”. Flashen afkøles hurtigere end resten af materialet; dette kølige metal er stærkere end metallet i matricen, så det hjælper med at forhindre, at der dannes mere flash. Dette tvinger også metallet til fuldstændigt at fylde matricehulen. Efter smedning fjernes flashen.
i kommerciel impression-die smedning flyttes emnet normalt gennem en række hulrum i en matrice for at komme fra en gødning til den endelige form. Det første indtryk bruges til at fordele metallet i den ru form i overensstemmelse med behovene i senere hulrum; dette indtryk kaldes et “kant”, “fullering” eller “bøjning” indtryk. Følgende hulrum kaldes” blokerende ” hulrum, hvor stykket arbejder i en form, der mere ligner det endelige produkt. Disse trin giver normalt emnet med generøse bøjninger og store fileter. Den endelige form er smedet i en” endelig “eller” efterbehandler ” indtryk hulrum. Hvis der kun er en kort række dele, der skal udføres, kan det være mere økonomisk for matricen at mangle et endeligt indtrykshulrum og i stedet bearbejde de endelige funktioner.Impression-die smedning er blevet forbedret i de senere år gennem øget automatisering, som omfatter induktionsopvarmning, mekanisk fodring, positionering og manipulation og direkte varmebehandling af dele efter smedning.En variation af indtryk-dør smedning kaldes” flashless smedning “eller”ægte lukket dør smedning”. I denne type smedning er hulrummene helt lukkede, hvilket forhindrer emnet i at danne flash. Den største fordel ved denne proces er, at mindre metal går tabt for at blinke. Flash kan tegne sig for 20 Til 45% af udgangsmaterialet. Ulemperne ved denne proces inkluderer yderligere omkostninger på grund af et mere komplekst dørdesign og behovet for bedre smøring og placering af emnet.
der er andre variationer af deldannelse, der integrerer impression-die smedning. En metode inkorporerer støbning en smedning præform fra flydende metal. Støbningen fjernes, efter at den er størknet, men mens den stadig er varm. Det er derefter færdig i en enkelt hulrum dør. Flashen er trimmet, så er delen slukket hærdet. En anden variation følger den samme proces som beskrevet ovenfor, bortset fra at præformen fremstilles ved sprøjteaflejring af metaldråber i formede samlere (svarende til Fiskeørnsprocessen).
smedning med lukket dør har en høj startomkostning på grund af oprettelsen af matricer og krævet designarbejde for at fremstille arbejdshulrum. Det har dog lave tilbagevendende omkostninger for hver del, og smedegods bliver således mere økonomiske med større produktionsvolumen. Dette er en af hovedårsagerne til, at smedegods med lukket dør ofte bruges i bil-og værktøjsbranchen. En anden grund til, at smedegods er almindelige i disse industrisektorer, er, at smedegods generelt har omkring 20 procent højere styrke-til-vægt-forhold sammenlignet med støbte eller bearbejdede dele af det samme materiale.
design af smedegods og værktøjredit
smedegods er normalt lavet af højlegeret eller værktøjsstål. Dies skal være slag-og slidstærk, opretholde styrke ved høje temperaturer, har evnen til at modstå cykler med hurtig opvarmning og afkøling. For at producere en bedre, mere økonomisk dør opretholdes følgende standarder:
- dørdelen langs et enkelt, fladt plan, når det er muligt. Hvis ikke, følger skilleplanet konturen af delen.
- skillefladen er et plan gennem midten af smedningen og ikke nær en øvre eller nedre kant.
- passende træk er tilvejebragt; normalt mindst 3 liter for aluminium og 5 liter til 7 liter for stål.
- Generøse fileter og radier anvendes.ribberne er lave og brede.
- de forskellige sektioner er afbalanceret for at undgå ekstrem forskel i metalstrøm.
- fuld fordel er taget af fiber strømningslinjer.
- Dimensionstolerancer er ikke tættere end nødvendigt.
tønde opstår, når arbejdsemnet på grund af friktion mellem arbejdsemnet og matricen eller stansen buler ud i midten på en sådan måde, at det ligner en tønde. Dette fører til, at den centrale del af arbejdsemnet kommer i kontakt med siderne af matricen hurtigere, end hvis der ikke var nogen friktion til stede, hvilket skaber en meget større stigning i det tryk, der kræves for stansen til at afslutte smedningen.
dimensionstolerancerne for en ståldel fremstillet ved hjælp af indtrykssmedemetoden er beskrevet i nedenstående tabel. Dimensionerne på tværs af skilleplanet påvirkes af lukningen af matricerne og er derfor afhængige af matriceslitage og tykkelsen af den endelige flash. Dimensioner, der er fuldstændigt indeholdt i et enkelt dørsegment eller halvdelen, kan opretholdes på et betydeligt større nøjagtighedsniveau.
dimensionelle tolerancer for impression-die smedegods masse Minus tolerance plus tolerance 0.45 (1) 0.15 (0, 006) 0, 46 (0, 018) 0, 91 (2) 0, 20 (0, 008) 0, 61 (0, 024) 2, 27 (5) 0, 25 (0, 010) 0, 76 (0, 030) 4, 54 (10) 0.28 (0, 011) 0, 84 (0, 033) 9, 07 (20) 0, 33 (0, 013) 0, 99 (0, 039) 22, 68 (50) 0, 48 (0, 019) 1, 45 (0, 057) 45, 36 (100) 0, 74 (0, 029) 2, 21 (0, 087) et smøremiddel anvendes ved smedning for at reducere friktion og slid. Det bruges også som en termisk barriere for at begrænse varmeoverførslen fra emnet til matricen. Endelig fungerer smøremidlet som en skilleforbindelse for at forhindre, at delen klæber i matricerne.
Tryk smedningedit
Tryk smedning arbejder ved langsomt at anvende et kontinuerligt tryk eller kraft, som adskiller sig fra den næsten øjeblikkelige virkning af drop-hammer smedning. Mængden af tid matricerne er i kontakt med emnet måles i sekunder (sammenlignet med millisekunder af drop-hammer smedjer). Pressen smedning operation kan gøres enten koldt eller varmt.
den største fordel ved pressesmedning sammenlignet med drop-hammer smedning er dens evne til at deformere det komplette emne. Drop-hammer smedning deformerer normalt kun overfladerne på arbejdsemnet i kontakt med hammeren og ambolten; det indre af emnet forbliver relativt uformet. En anden fordel ved processen inkluderer viden om den nye parts belastningshastighed. Ved at styre kompressionshastigheden af pressen smedning operation, kan den interne stamme styres.
der er et par ulemper ved denne proces, hvoraf de fleste stammer fra, at emnet er i kontakt med matricerne i en så lang periode. Operationen er en tidskrævende proces på grund af mængden og længden af trin. Emnet afkøles hurtigere, fordi matricerne er i kontakt med emnet; matricerne Letter drastisk mere varmeoverførsel end den omgivende atmosfære. Når emnet afkøles, bliver det stærkere og mindre duktilt, hvilket kan fremkalde revner, hvis deformationen fortsætter. Derfor bruges opvarmede matricer normalt til at reducere varmetab, fremme overfladestrøm og muliggøre produktion af finere detaljer og tættere tolerancer. Arbejdsemnet skal muligvis også genopvarmes.
når det gøres i høj produktivitet, er pressesmedning mere økonomisk end hammersmedning. Operationen skaber også tættere tolerancer. Ved hammer smedning absorberes meget af arbejdet af maskinen; når man er i pressesmedning, bruges den større procentdel af arbejdet i arbejdsemnet. En anden fordel er, at operationen kan bruges til at skabe enhver størrelse del, fordi der ikke er nogen grænse for størrelsen af pressen smedning maskine. Nye pressesmedningsteknikker har været i stand til at skabe en højere grad af mekanisk og orienteringsintegritet. Ved begrænsningen af iltning til de ydre lag af delen forekommer reducerede niveauer af mikrokrakning i den færdige del.
Tryk smedning kan bruges til at udføre alle former for smedning, herunder åben-dør og indtryk-dør smedning. Impression-die press smedning kræver normalt mindre udkast end drop smedning og har bedre dimensionel nøjagtighed. Også, tryk smedegods kan ofte gøres i en lukning af matricer, giver mulighed for nem automatisering.
forstyrret smedningedit
“forstyrrende” omdirigeringer her. For alternative betydninger, se forstyrret (flertydig).Upset smedning øger diameteren af emnet ved at komprimere dens længde. Baseret på antallet af producerede stykker er dette den mest anvendte smedningsproces. Et par eksempler på almindelige dele produceret ved hjælp af den forstyrrede smedningsproces er motorventiler, koblinger, bolte, skruer og andre fastgørelseselementer.
Upset smedning udføres normalt i specielle højhastighedsmaskiner kaldet krumtappresser. Maskinerne er normalt indstillet til at arbejde i vandret plan for at lette hurtig udveksling af emner fra en station til den næste, men forstyrrende kan også udføres i en lodret krumtappresse eller en hydraulisk presse. Det oprindelige emne er normalt tråd eller stang, men nogle maskiner kan acceptere stænger op til 25 cm (9,8 tommer) i diameter og en kapacitet på over 1000 tons. Standard forstyrrende maskine anvender split dør, der indeholder flere hulrum. Matricerne er åbne nok til, at emnet kan bevæge sig fra det ene hulrum til det næste; dørene lukkes derefter, og overskriftsværktøjet eller rammen bevæger sig derefter i længderetningen mod stangen og forstyrrer det i hulrummet. Hvis alle hulrum udnyttes på hver cyklus, vil der blive produceret en færdig del med hver cyklus, hvilket gør denne proces fordelagtig til masseproduktion.
disse regler skal følges ved design af dele, der skal forstyrres smedet:
- længden af ikke-understøttet metal, der kan blive forstyrret i et slag uden skadelig buckling, bør begrænses til tre gange diameteren af stangen.
- længder af lager større end tre gange diameteren kan blive forstyrret med succes, forudsat at diameteren af forstyrrelsen ikke er mere end 1,5 gange diameteren af bestanden.
- i en forstyrrelse, der kræver lagerlængde større end tre gange diameteren af bestanden, og hvor hulrummets diameter ikke er mere end 1,5 gange diameteren af bestanden, må længden af ikke-understøttet metal ud over overfladen af matricen ikke overstige barens diameter.
automatisk hot smedningedit
den automatiske hot smedning proces involverer fodring Mølle-længde stålstænger (typisk 7 m (23 ft) lang) i den ene ende af maskinen ved stuetemperatur og varme smedede produkter frem fra den anden ende. Alt dette sker hurtigt; små dele kan fremstilles med en hastighed på 180 dele pr.minut (ppm) og større kan fremstilles med en hastighed på 90 ppm. Delene kan være faste eller hule, runde eller symmetriske, op til 6 kg (13 lb) og op til 18 cm (7,1 tommer) i diameter. De vigtigste fordele ved denne proces er dens høje Outputhastighed og evne til at acceptere billige materialer. Der kræves lidt arbejde for at betjene maskinen.
der produceres ingen flash, så materialebesparelser er mellem 20 og 30% i forhold til konventionel smedning. Slutproduktet er en konsistent 1.050 liter C (1.920 liter F), så luftkøling vil resultere i en del, der stadig er let bearbejdelig (fordelen er manglen på udglødning, der kræves efter smedning). Tolerancer er normalt 0,3 mm (0,012 tommer), overflader er rene, og trækvinkler er 0,5 til 1 liter. Værktøjslevetiden er næsten det dobbelte af konventionel smedning, fordi kontakttiderne er i størrelsesordenen 0,06 sekund. Ulempen er, at denne proces kun er mulig på mindre symmetriske dele og omkostninger; den oprindelige investering kan være over $10 millioner, så der kræves store mængder for at retfærdiggøre denne proces.
processen starter med at opvarme stangen til 1.200 til 1.300 liter C (2.190 til 2.370 liter F) på mindre end 60 sekunder ved hjælp af højeffektive induktionsspoler. Det afkalkes derefter med ruller, skæres i emner og overføres gennem flere på hinanden følgende formningstrin, hvor det er forstyrret, præformet, endelig smedet og gennemboret (om nødvendigt). Denne proces kan også kobles med højhastighedskolddannende operationer. Generelt vil koldformningsoperationen gøre efterbehandlingstrinnet, så fordelene ved koldbearbejdning kan opnås, samtidig med at den høje hastighed ved automatisk varm smedning opretholdes.
eksempler på dele fremstillet ved denne proces er: hjulnav enhed lejer, transmission gear, koniske rullelejer løb, rustfrit stål kobling flanger og hals ringe til LP gasflasker. Manuel gearkasse gear er et eksempel på automatisk varm smedning, der anvendes i forbindelse med koldbearbejdning.
Roll smedningedit
Roll smedning er en proces, hvor runde eller flade bar lager reduceres i tykkelse og øges i længden. Roll smedning udføres ved hjælp af to cylindriske eller halvcylindriske ruller, der hver indeholder en eller flere formede riller. En opvarmet stang indsættes i rullerne, og når den rammer et sted, roterer rullerne, og stangen formes gradvist, når den rulles gennem maskinen. Stykket overføres derefter til det næste sæt riller eller vendes om og genindsættes i de samme riller. Dette fortsætter, indtil den ønskede form og størrelse er opnået. Fordelen ved denne proces er, at der ikke er nogen flash, og det giver en gunstig kornstruktur i emnet.
eksempler på produkter fremstillet ved hjælp af denne metode omfatter aksler, koniske håndtag og bladfjedre.
net-shape og near-net-shape smedningedit
Se også: Near-net-shapedenne proces er også kendt som præcision smedning. Det blev udviklet for at minimere omkostninger og affald forbundet med post-smedning operationer. Derfor kræver det endelige produkt fra en præcisionssmedning ringe eller ingen endelig bearbejdning. Omkostningsbesparelser opnås ved brug af mindre materiale og dermed mindre skrot, det samlede fald i den anvendte energi og reduktion eller eliminering af bearbejdning. Precision smedning kræver også mindre af et udkast, 1 Lot til 0 lot. Ulempen ved denne proces er dens omkostninger, derfor implementeres den kun, hvis der kan opnås en betydelig omkostningsreduktion.
kold smedningredit
nær netform smedning er mest almindelig, når dele smedes uden opvarmning af slug, bar eller billet. Aluminium er et almindeligt materiale, der kan være koldt smedet afhængigt af den endelige form. Smøring af de dele, der dannes, er afgørende for at øge parringsdysernes levetid.
induktion smedningrediger
Hovedartikel: Induktionssmedningi modsætning til ovenstående processer er induktionssmedning baseret på den anvendte type opvarmningsstil. Mange af de ovennævnte processer kan anvendes i forbindelse med denne opvarmningsmetode.
Multidirectional smedningedit
Multidirectional smedning danner et emne i et enkelt trin i flere retninger. Den multidirektionelle formning finder sted gennem konstruktive foranstaltninger af værktøjet. Den lodrette bevægelse af pressestammen omdirigeres ved hjælp af kiler, der distribuerer og omdirigerer kraften i smedepressen i vandrette retninger.
isotermisk smedningredit
isotermisk smedning er en proces, hvorved materialerne og matricen opvarmes til samme temperatur (iso – betyder “lige”). Adiabatisk opvarmning bruges til at hjælpe med deformation af materialet, hvilket betyder, at belastningshastighederne er stærkt kontrollerede. Almindeligt anvendt til smedning aluminium, som har en lavere smedning temperatur end stål. Smedningstemperaturer for aluminium er omkring 430 liter C (806 liter F), mens stål og superlegeringer kan være 930 til 1.260 liter C (1.710 til 2.300 liter F).
fordele:
- i nærheden af netformer, der fører til lavere bearbejdningskrav og derfor lavere skrothastigheder
- reproducerbarhed af delen
- på grund af det lavere varmetab kan mindre maskiner bruges til at fremstille smedningen
ulemper:
- højere matricematerialomkostninger til håndtering af temperaturer og tryk
- ensartede varmesystemer er påkrævet
- beskyttende atmosfærer eller vakuum for at reducere iltningen af matricerne og materialet
- lave produktionshastigheder
Leave a Reply